在冷冻食品行业中,由于各制造商的托盘规格不同,导致在供应链上的托盘化作业进展不顺。此外,与其他温区相比,冷冻物流设施内的劳动环境更为恶劣,但依靠人力完成装卸货的问题仍未得到解决。由此,卡车司机长时间在交货地点的等待问题已成为社会问题,这也成了阻碍冷链物流稳定运营的风险因素。为解决这些问题,日本Access公司作为全渠道批发商,构建了涵盖所有温层的独特物流体系。在2022财年,作为新的物流战略,推出了“冷冻母中心”,这一举措,作为提高冷链效率和合理化的新途径,获得了高度评价。因此,本刊询问了该公司物流战略室室长田中弘志,他是这一新概念的关键人物,了解从新概念提出到中心运营的背景和角色,并受邀参观了这个备受瞩目的中心内部流程。
颠覆批发业的常识
勇敢挑战进入制造商二次物流的领域
Access作为日本知名的冷链物流企业,其拥有的“冷冻母中心”在由日本国土交通省和经济产业省共同实施的物流伙伴关系优秀企业表彰中,获得了“物流结构改革表彰”。那该物流配送中心是经历了什么才成立的呢?
田中弘志表示,众所周知,冷冻食品的物流与其他行业相比,工作环境并不是很好。首先,工作区域处于对身体负担较大的温度区。在托盘化作业还没有取得进展的情况下,卡车司机需要在工厂和收货地点分别需要花费各2小时进行手工装卸货物。另外,作为接收方的物流配送中心也面临着车辆在泊位上长时间装卸货,导致的设施没有空闲泊位的问题,这也为Access公司带来了“去Access的物流配送中心总是要等待”的负面评价,并且引起制造商的投诉。
如果货物能用托盘运送,那么装载和卸货都可以在短时间内完成,因此Access曾多次请求制造商“请使用托盘来交付货物”,但托盘交付很难实现,而且这样的情况已经持续了很长时间。在这种情况下,尤其是进入司机短缺时代之后,冷链物流司机更是变得寥寥无几了。若放任不管的话,势必也将影响整个冷链食品的供应链运营。
“尤其是对于Access而言,冷冻产品的销售占比非常高,因此与其他企业相比,冷链物流是一个十分重要的项目。”田中弘志继续道,“如今这个重要项目的供应链物流正在面临严重的威胁,我们就这样视而不见。”也正是如此,Access内部达成了一个共识,如果直接向制造商施压也不能促进托盘化作业的实际进展,那么就由自己亲自来推动这项工作。具体而言,Access将承担起以往属于制造商领域的二次物流(从销售仓库到客户中心的物流)工作。也就是说,Access等批发商尝试踏入制造商的物流领域,这就是Access所提出的冷冻母中心构想的具体体现(见图表1)。
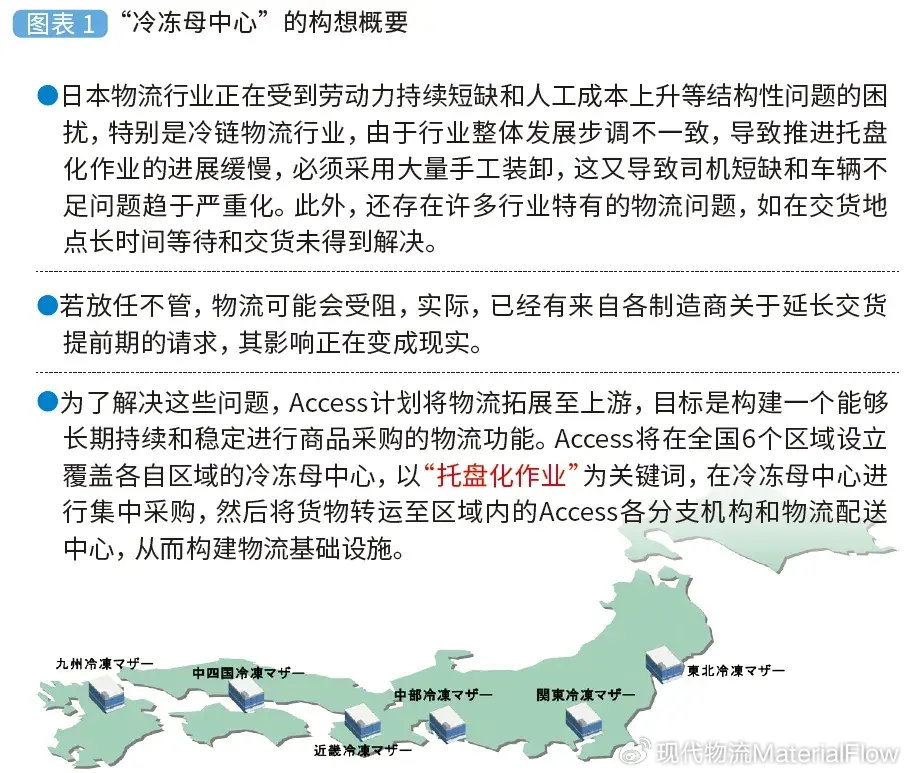
想要能够继续推动托盘化作业,需要Access打破持续已久包括商流在内的流程习惯。但是,这也会让Access面临其他的风险。当制造商将商品送达母中心后,这些商品就成为Access的库存。从企业经营的角度来看,此举意味着需要承担库存风险等多方面的负面影响。但即便如此,Access还是得出了不能就这样放任不管的结论。“我确实认为,当时的管理层能做出这样的判断是非常明智的。”田中弘志由衷地说道。
但益处也是十分明显。因为从制造商那里收货后,就变成了Access内部的物流,因此,从各地的冷冻母中心到Access公司的物流配送中心的移动,可以视为在公司内部转移库存,这样Access就可以按照自己的流程来进行操作了。据田中弘志介绍,目前Access服务的客户大约有10家冷冻食品制造商和9家冰淇淋制造商。最初是从6到15家公司一起开始的,但制造商的第一反应是:“Access公司想做什么?”
利用托盘化
将等待时间减少到四分之一
大约在2019年4月份,Access决定要打破传统,进行二次物流并启动对冷冻母中心的讨论。至2020年11月,关东冷冻母中心开始了预运行。冷冻母中心计划在全国设立6个基地,日本近畿地区从2023年3月开始运营,日本中国地区(鸟取县、岛根县、冈山县、广岛县、山口县5个县)、四国地区已经开始运作。
Access最终的目标是如图表2所示的状态。表格上部分是当前的物流状况,商品从制造工厂运送到销售仓库,然后再送往物流中心。其中关于冷冻食品制造商的情况,在工厂里商品虽然是放在托盘上储存的,但在运输到自家的销售仓库时却特意散装在卡车上。而且,尽管在销售仓库商品储存时也是放在托盘上,但从那里送往物流配送中心时又会再次散装堆放。
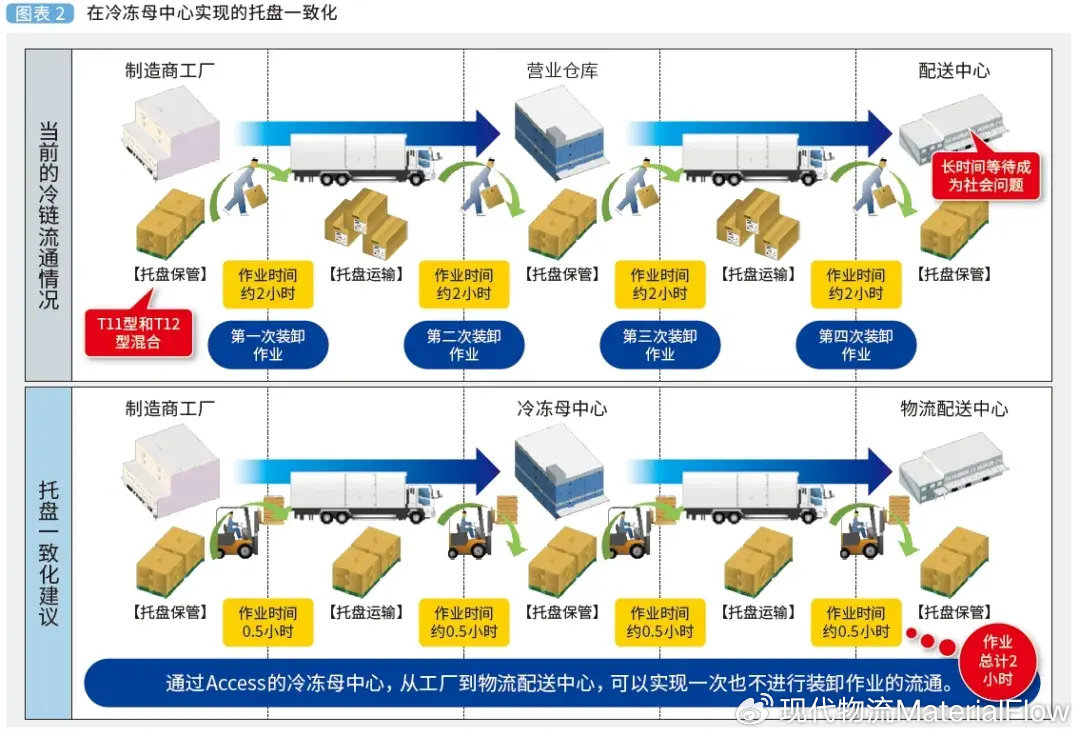
由于销售仓库的托盘是销售仓库的资产,所以他们不愿意把托盘带出去。造成的结果就是,商品在到了物流配送中心之后也是以散装形式交付的。因此,在商品到达消费者之前,会产生4次的装卸作业,如果每次装卸需要2小时,那么总共会产生8小时的工时,这本应是不必要的。
另一方面,在图表下面的冷冻母中心,Access会要求制造商从工厂到冷冻母中心全程使用托盘运输。此外,从冷冻母中心到Access物流配送中心也将全部使用托盘运输。这一实施后,装卸作业将缩短至30分钟,司机被占用的时间也将大约减少到原来的四分之一。
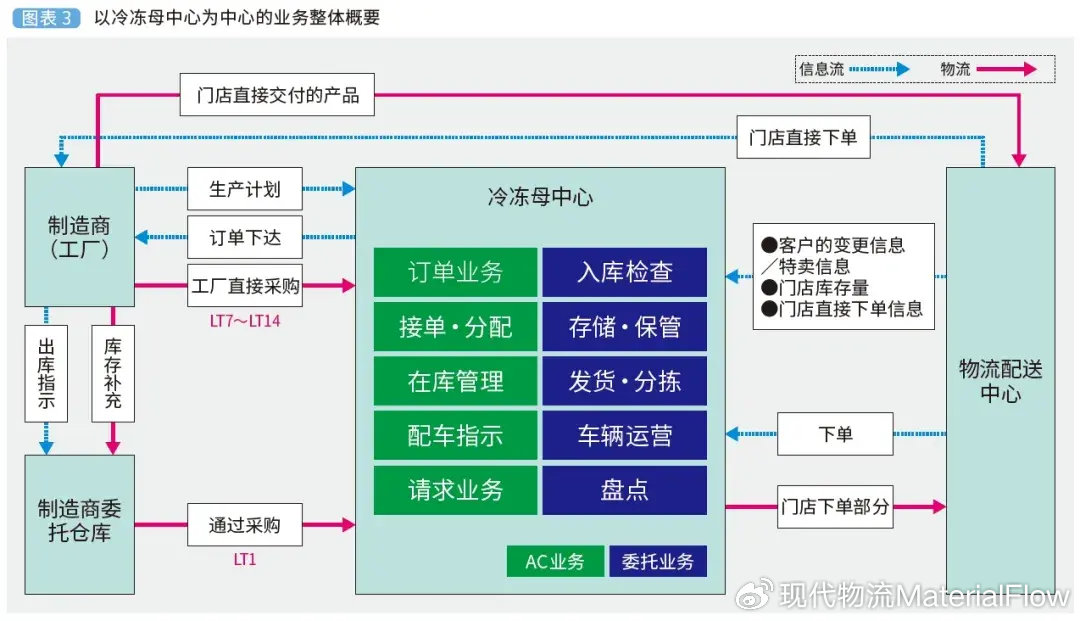
接着,田中弘志介绍了对于信息流和物流的整合。以图表3为例,蓝色线条表示信息流,红色线条为物流。总体而言,制造商接收到来自冷冻母中心订单后,工厂将会根据订单要求将商品送入冷冻母中心。从冷冻母中心到Access物流配送中心也是同样的流程,物流配送中心向冷冻母中心下达订单,然后根据这些信息,按照分店的订单交付货物。
在实际运作过程中,Access已经获得了由制造商披露的生产计划,并根据这个计划从冷冻母中心下订单。基本上Access采取了一种体系,即所有商品都直接从工厂采购到冷冻母中心。每个工厂的库存空间都是有限的,而且本来工厂就是用来生产商品的地方,不是用来储存的,所以一旦生产出来就必须尽快出货,否则生产就会停滞。因此,根据生产计划从冷冻母中心下订单,就意味着从工厂生产在线出来的商品可以立即被送往冷冻母中心。
到目前为止,该方案已经在与大多数冰淇淋制造商的合作中实现了,但还没有一家冷冻食品制造商能够实现。其原因可能是他们非常重视装载率可能下降的问题。如果是散装,可以将货物堆满到卡车的顶部,但如果使用托盘,就无法堆积到那么高,所以从工厂出发的车辆的装载率据说会下降到大约70%,这是最大的障碍。相比之下,田中弘志认为冰淇淋制造商从一开始就建立了基于托盘装载率的生产体制。
通过自营化能够控制订购单
从而实现整体最优化
在托盘化作业的推动进程方面,田中弘志以图表4总结了为实现该行动而进行的工作。以制造商与“冷冻母中心”的沟通为例,首先会请制造商披露下月的生产计划,然后在当前时间点上下达订单。如此工厂就可以避免不必要的库存,而且产品一旦生产完毕,就能立即将其运送到冷冻母中心。
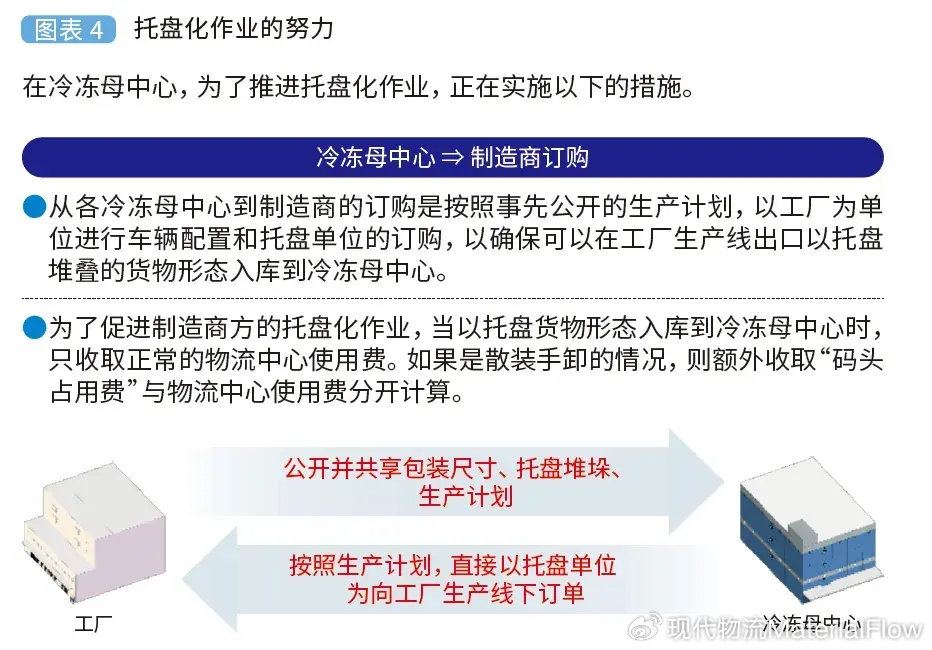
对此,Access采取了几个巧妙的措施。首先,由于制造商在工厂中也是将产品堆放在托盘上,因此如果能够将这些已经堆放好的产品直接装载到车辆上带到冷冻母中心,就可以减少工厂内的额外装卸工作。因此,当冷冻母中心向制造商下订单时,订单数量是按照工厂暂时存放时托盘堆栈的倍数进行的。此外,通过一次性下订单购买多达16个托盘的产品,Access还巧妙地安排了订单,以确保与传统相比,制造商的一级物流费用不会增加。
另外,对于那些不用托盘而是零散交付商品的制造商,Access实施了另一种方案,按照与使用托盘交付时中心利用费不同的标准进行收费。然而,实际情况是,尽管需要支付额外费用,仍然有许多制造商倾向于零散地交付商品。此外,还有一个问题就是,即使在冷冻母中心体系内实现托盘化作业,但是最终交付给零售终端和最后一公里的过程中,还是要执行去托盘化的步骤,这难道不会导致冷冻母中心的流程和工作量增加吗?对此,田中弘志表示至少在其他流程中的工作量不会增加,虽然终端使用者很少使用托盘,但到目前为止流程还是十分流畅。
关于冷冻母中心与分支物流配送中心的运作情况,田中弘志表示Access希望尽可能地使用托盘完成运作。由此,Access为每个分支物流配送中心的每个项目设置了订购单位(见图表5)。以L公司的冰淇淋产品为例来说明,这个产品一个托盘上可以放128箱,所以如果能以128的倍数进行订购,Access就可以按托盘单位来发货。
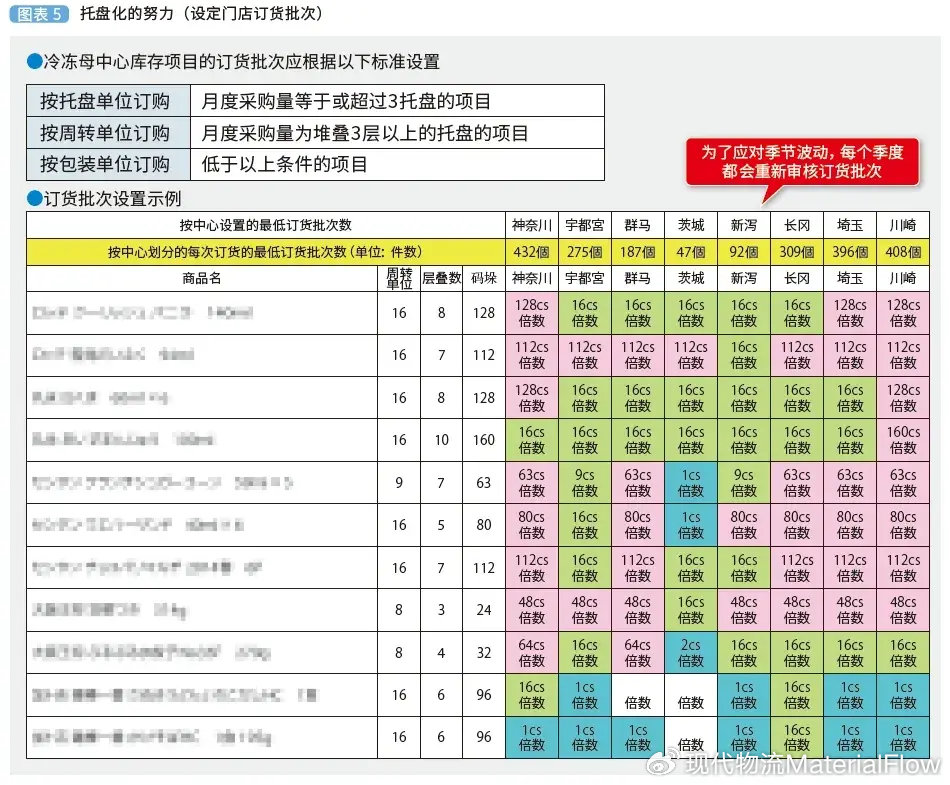
在这样的情况下,像神奈川、埼玉、川崎这样的大型物流配送中心,即使按128的倍数下订单,库存也不会增加太多。但对于像宇都宫、群马、茨城这样的小型物流配送中心来说,如果真的按照托盘的倍数来订购,库存就会过多。在这样的分支机构,Access会要求按“回转单位”的倍数来下订单。
通过说服进行调整与克服
比外部更强大的“内部抵抗力”
田中弘志解释道,“回转单位”是指托盘上堆放时的一层,即为了实现托盘化,需要像图表6右侧照片那样堆放。通过这种方式,如果最顶部的高度不均匀,托盘就无法有效使用。因此,如果无法以一个托盘为单位进行订购,Access会要求以一个托盘的一层,也就是“回转单位”进行订购。
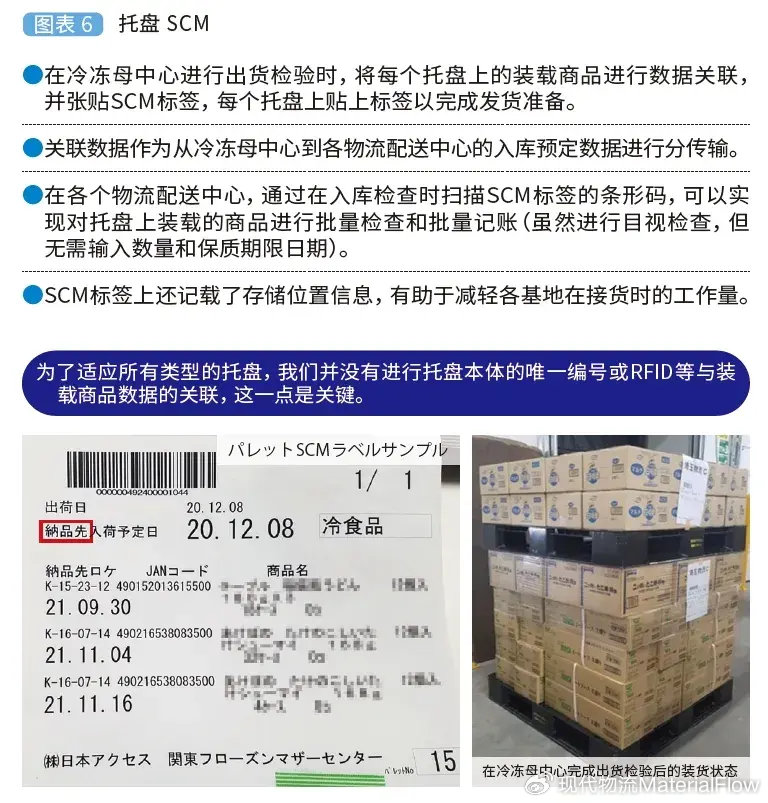
在这之前,因为不需要考虑托盘化作业的问题,各中心向制造商订货都是以箱为单位的。因此关于托盘化作业的抵触情绪是确实存在的。甚至比起制造商的反应,Access内部更有很大的反对声音,比如“为什么过去能够以一箱为单位下订单,现在却要求以16箱或者128箱这样的大批量来下订单”。而且虽然公司内部的调整可以通过自上而下的方式进行推进,但Access能够推行还有其他的原因。
田中弘志表示,从整体运营的效率来看,每天订购一箱的情况是最低效的。因为在这样的情况下,会导致在库商品中含有多个不同保质期的情况,由此库存管理会变得复杂且困难,而且每天都要进行小批量的入库检验和存储工作。而在转变为“一周一次”的订单频率下,每周都能够收到一定量的商品,由此接收方的工作与管理效率也会更加高效。而且,由于所有商品都是放在托盘之上,所以可以直接入库上架保存。若要在以前,需要将各种商品以箱为单位放到不同的储位,相比之下往返一次操作就能同时存放几十箱明显效率更高。这些都是Access用来说服各个物流配送中心的关键原因。
话虽如此,Access也不能仅仅把总部的逻辑强加给各个中心。因此,Access制定了一定数量单位的规则。比如,与各个中心逐一约定,那些传统上每次入库超过三个托盘的商品,之后将全部改为按托盘单位入库。考虑到冻品的重量偏大,Access总部也采取了相应的措施,尽量保证不会将过重的商品放置在托盘上。
无需检验的内部库存转移
托盘化的巨大效果体现
接着,田中弘志讲述了托盘化作业的效果。其中图表6展示了Access内部范围无需检验的机制。在冷冻母中心的出货检验作业中,在出货时采用手持终端进行扫码对每个订单的日期和数量进行检验。该项作业十分简单,将一个商品的条形码作为一个整体进行计数,作业人员只需要通过目视检查与订单数量是否相符,然后按下手持设备上的OK按钮。Access在应用到托盘上时,对第一层托盘的两个项目进行扫描并检查保质期和数量,在确认没有问题按下OK键后,将会打印记录刚刚检验过的两个项目的信息卷标。
之后只要将标签贴在托盘上,出货准备就完成了。通过这种方式从冷冻母中心到各个物流配送中心的货物,在到达收货方进行入库检验时,只需检查标签上的条形码就可以确认该托盘上的商品一次性全部入库。因为是在公司内部体系转移,所以大家都认为“在到达收货方无需做入库检验”是没有问题的,Access也就建立了这样的系统。
就目前而言,从冷冻母中心出发的车辆都是以满载的状态前往各个物流配送中心,单辆车完成所有商品的卸货到入库检验的时间只需要20~25分钟,现场效率非常高。放在以前,所有货物需要重新放置到托盘上,然后再对每个托盘进行扫描和检查数量和日期,整个作业需要2个小时,这样司机也同样需要等待2个小时。
同时,Access还要考虑到商品的效期管理与检验等关键事宜。为此,Access在采购阶段就考虑到了商品的效期管理与检验,虽然在物流配送中心交付时也可能会发生数量不准确或外包装损坏的情况,但是Access规定了由冷冻母中心承担所有的差错。这样的目的是使整个供应链流程更加顺畅,Access希望减少公司内部不必要的往来,如果还要再对已经由托盘形式送来的货物进行重新检验,不如在有预期的缺货或问题发生后,有冷冻母中心来承担和解决,这对整体效率最优化更有贡献。
当然,田中弘志坦承道,虽然进行托盘化作业的意义就在于此,但是能够推行起来的关键在于这些业务都在同一个公司的内部进行,如果将这样的体系延伸到其他企业,情况会变得不那么顺畅。“在冷冻母中心,如果商品不是以Access名义的存储,该方案就无法成立。如果是以制造商名义仓储,就要重新入库,这就意味着发生了交易。我们希望能够改变这个流程,但在最初各个制造商很难理解这一点。”田中弘志继续道,“当然冷冻母中心的项目能够顺利进行,管理层的理解和支持是主要动力。从优化供应链效率的角度出发,管理层甚至作出了即便持有库存也无妨的决策,这也是成功的关键所在。”
率先投入自有托盘
不惜成本负担来推动谈判
另一方面,托盘化作业中由谁来承担托盘的成本也是关键问题。对此Access在行动之初就购买了5,000个托盘,专门用于总部的运营,总部将其作为公司的资产来管理,从而避免因对成本负担无法达成一致,从而导致托盘一贯化失败。因此Access决定自己主动提供托盘,从而让谈判更加顺畅,而事实证明这样的投入是十分有价值的。
谈及日本冷冻食品的市场的现状和展望,田中弘志表示市场未来持续增长是肯定的,由于食品浪费(因过期而造成的浪费)已经成为一个社会问题,因此食品冷冻化将会成为一个关键趋势,这也将有助于延长食品保质期从而减少食品浪费。从这点看,冷链物流的需求肯定还将不断增长。“这正是我们希望看到的,并且我们认为有必要不断地改进冷冻母中心的工作和操作,使之与各个现场的实际情况相适应。”田中弘志说道。
例如,在关东启动的冷冻母中心全面展开的第二阶段中,最近在近畿地区开设的中心内,改变了托盘堆放时的高度。在关东,存储时托盘的高度设定为1,500mm,而在近畿则设定为1,100mm。实际上,近畿有4个物流中心已经引入了托盘自动仓库,每个物流中心的自动仓库存储时的高度都在1,100mm左右,因此不得不将高度统一。
然而,这带来了意料之外的好结果。由于高度变为了1,100mm,这使得在给车辆以托盘为单位装载时,能够堆栈两个标准托盘,这是在关东无法实现的。因此,可以两层全满地堆栈32个托盘,从而提高了运输效率。
另一个好处是,当高度为1,500mm时,订货单位是128箱,而将高度改为1,100mm后,即使是相同的商品,订货单位也可以降低到大约90箱,这使得订货更加容易进行整合。由此,在关东以满托盘状态出货的比例为75%,而在近畿这一比例甚至高达96%,几乎全部实现了满托盘状态的出货。“因此,我认为随着现场运营改善的持续推进,冷冻母中心的工作还有很大的改进空间。”随后,田中弘志带着本刊记者参观了冷冻母中心内部,下文是相关报导。