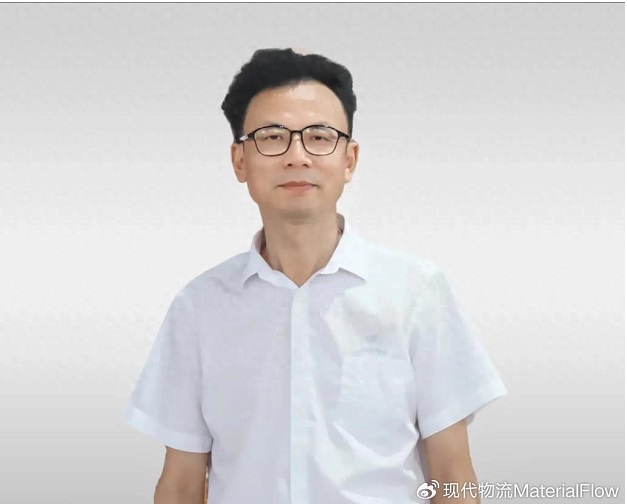
浙江利中汽车底盘件有限公司副总裁 花金荣
27,000个配件SKU,通过不同工艺和流程,组装成近10万个不同的成品SKU。尽管这只是汽车零部件制造业中的常态,但如何在这种常态下,将企业运营梳理得井井有条并且能够紧紧跟随市场趋势的步伐,这对于不同企业而言有着不同的想法和做法。本文报道的利中底盘件,其对于数字化、信息化转型的投入和理解,十分值得学习,亦称得上是行业标杆。
01
稳中有升的背后是“坚持”
几年前,本刊曾受普罗格邀约前往浙江利中汽车底盘件有限公司(全文简称:利中底盘件),采访了副总裁花金荣。彼时的利中底盘件虽然营收规模在行业内并不出众,不过其在“精益制造”方面的理解和实践却令人大为震撼。
如今数年过去,经历了疫情、市场等多重影响利中底盘件,又取得了什么样的发展呢?“稳中有升”,这是花金荣给出的回答。过去几年,利中底盘件一直以5%~8%的速度保持增长态势,能够取得如此稳定的业绩,花金荣表示要归功于利中底盘件的“坚持”。
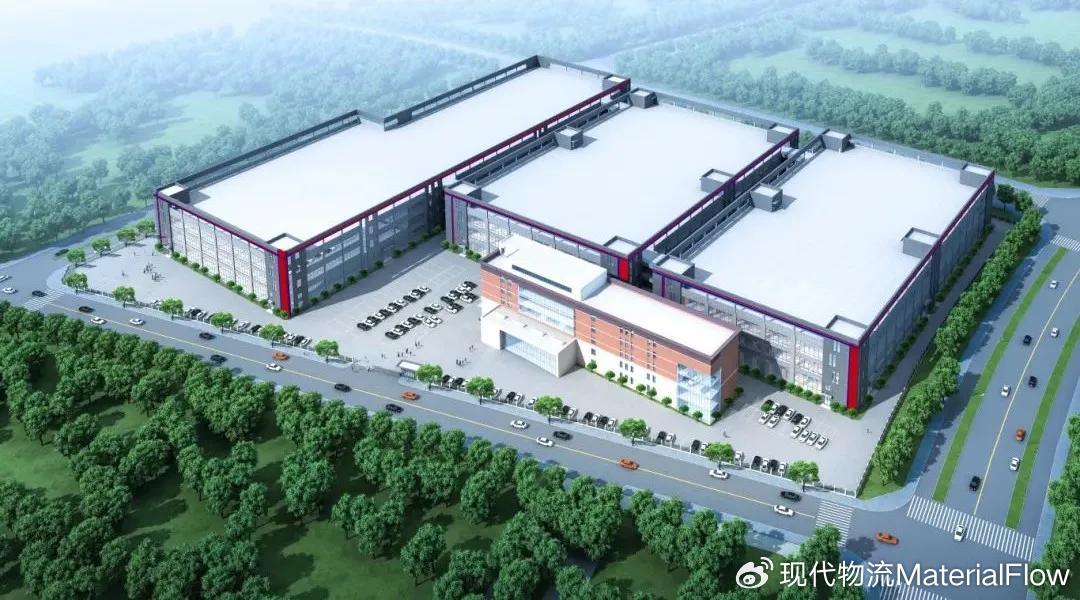
深耕汽车配件行业
自创立以来,利中底盘件在38年的时间里坚持专业生产制造汽车配件,如此之高的专注度让利中底盘件具备了专业、深厚的制造技术,也让其与客户建立了十分稳定的合作关系。花金荣进一步说道:“利中底盘件主要服务于国际市场,因此尽管国际贸易的形势十分严峻,但我们依然能够保持稳定的增长。”
02
客户需求变化沧海桑田驱动企业供应链不断升级优化
当然,这38年来市场的变迁亦是沧海桑田,汽车零部件制造也跟随着客户订单从“规模化”走向“小批量、多品种”。过去,这两种订单模式最直观地呈现在于“成本”之上,后者因客制化程度高而导致成本高也是行业现象。而进入到工业4.0时代,小批量、多品种的订单模式也在“降本增效”的趋势下,让制造企业在订单交付时面临了更大的挑战。
提升管理颗粒度实现低成本、精准交付
对此,花金荣分析道:“小批量、多品种的直接原因是客户不再愿意承担更多的库存成本,这也是VMI模式在汽车产业十分常见的原因之一。对于利中底盘件而言,由于主要客户市场远在海外,受到地理因素的影响,更需要在合适的成本上进一步提升每个订单管理的颗粒度,才能为后续运输交付提供更多的冗余,从而实现精准交付。”
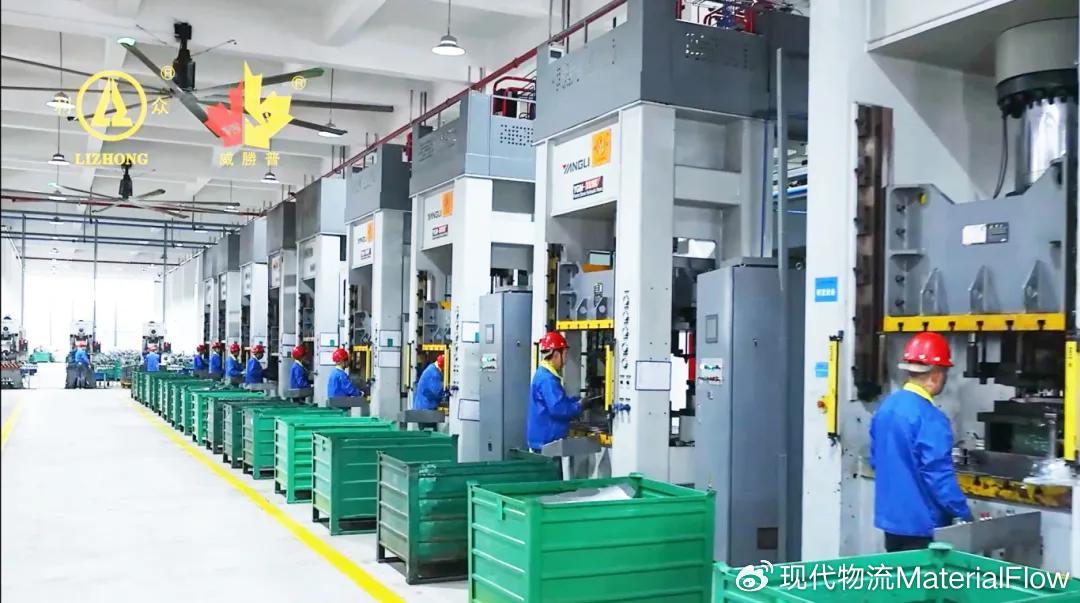
如此之下,利中底盘件持续增加零部件的SKU数量并且达到了27,000个,通过对这些零部件的“组合”(即生产制造)形成近10万个SKU的成品,并且能够可以同时接受客户不同批量(从个位数到上万)的订单需求。这个效果仅用文字描述似乎并不复杂,而利中底盘件为此投入的精力和时间贯穿了自身的发展历程。
利中的见解:“精益”管理三要素
在过去的报道中,利中底盘件展示了其在精益制造方面的结果,花金荣更是通过持续推进精益制造总结出了成功“三要素”:第一,基础数据具备极高的准确性;第二,合理、完整的流程管理;第三,以前两点为基础导入后的系统可以准确、高效地执行命令。在此基础上,利中底盘件仍在不断地提升管理的颗粒度,以生产计划为例,其管理的颗粒度达到了小时级别。由此,利中底盘件对于每个客户的订单交付计划同样实现了小时级别的管理,进一步提升了计划的达成率。花金荣进一步解释道,如此级别的颗粒度能够让利中底盘件在订单排程、物流计划方面更加游刃有余,这是近年来公司经营的一大发展成果。
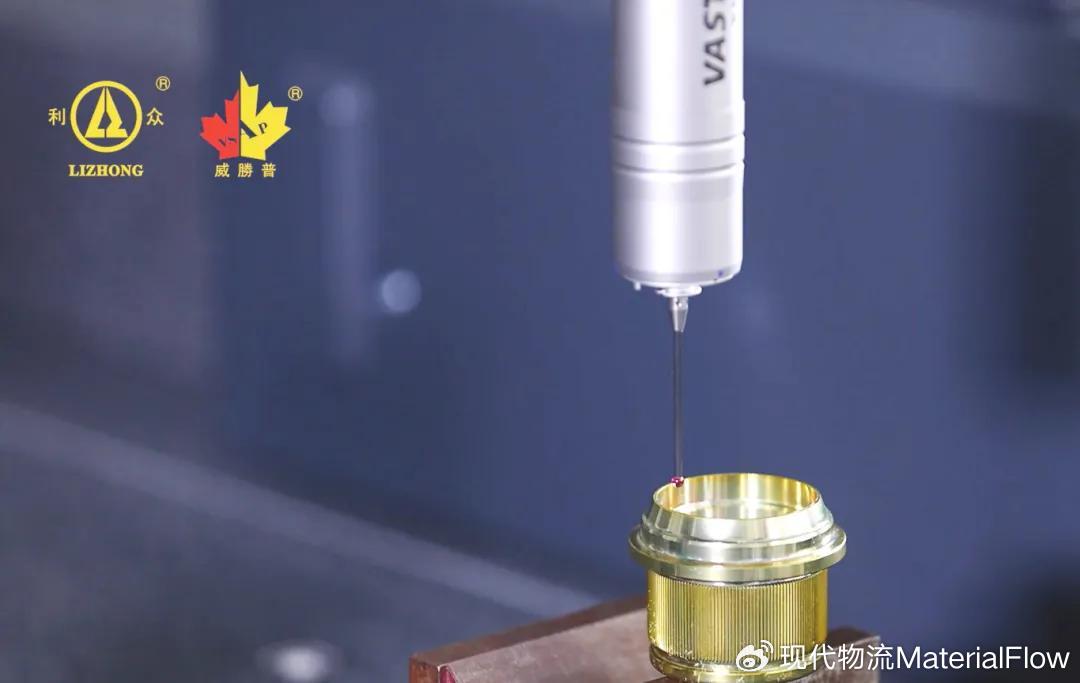
“小时级别”的计划管理
同时,公司的信息进一步透明化,计划部能够作为神经中枢站在客户的角度努力推动计划达成率,并对未达成的订单进行分析和整理,而且可以直观地干预订单生产,从而调整客户的交期。由此,所有生产订单的工作计划得以进一步清晰和明了,例如零部件的供应也被调整到小时级别,进一步提升了管理效率。
03
全流程信息化的投入与价值体现
这样的成果在行业内并不多见,相比于多数企业仍处于局部的自动化、信息化改造进程,能够实现全流程信息化的利中底盘件已经为行业下一步的发展提供了意义巨大的参考价值。
正确认识数字化的价值
花金荣坦言,企业对于数字化、信息化的投入是巨大的,不过所产生的价值也是十分可观的。但橘生淮南则为橘,橘生淮北则为枳,在企业推进数字化、信息化过程中,相当一部分的信息系统便成了“橘”,各行业内亦有“不上ERP是等死,上ERP是找死”的谬论。“产生这种谬论的直接原因是企业没有体会到其产生的价值。”花金荣继续道,“我们通过这三年的持续升级转型,越来越感受到清晰、准确、规范的数据管理对我们运营效率的提升,例如我们能够更有效地控制成本,让成本不再是‘小批量、多品种’的阻碍等。”
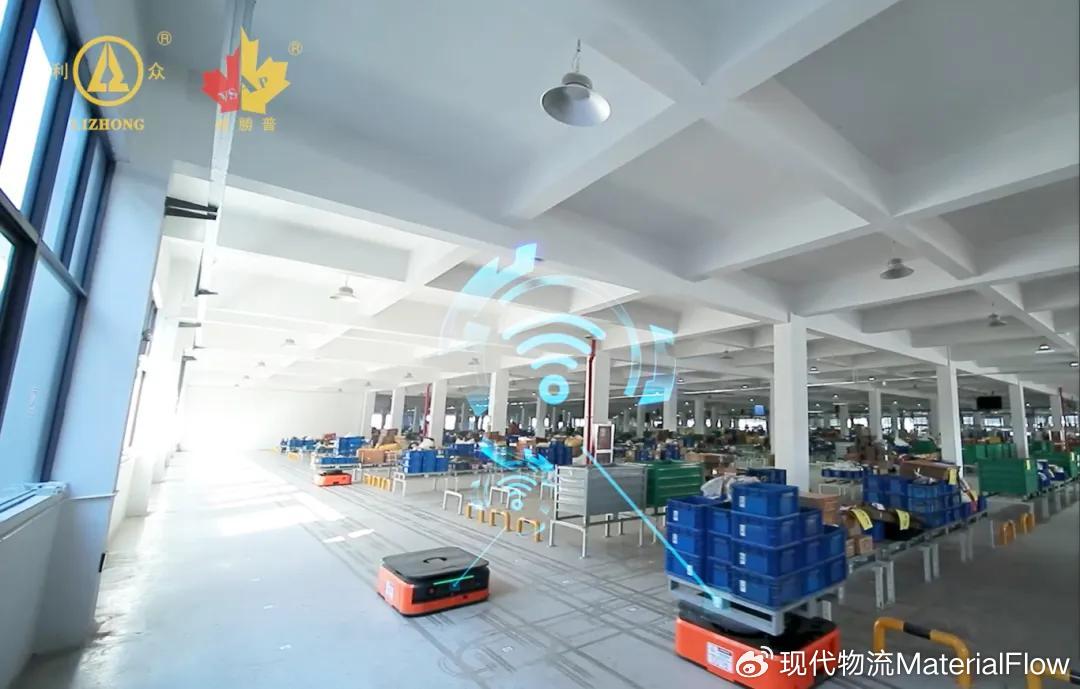
消除各系统的壁垒
另一大原因在于部分企业尽管已经推进了这方面的建设,但信息系统之间没有打通,数据不能够有效流转,这种浮于表面的建设只是让企业完成了无纸化转型。这两个因素导致企业管理层无法感受到数字化、信息化的价值,也就从源头失去了转型的动力。“我们的管理层十分开放,且具备了开拓精神,我也曾在这个过程中,不断地与团队从战略到战术亲力亲为,从而达到了现在的效果。”
流程规划成功的关键在于“诉求明确”
其中关键的难点在于如何与企业实际运营(包括生产制造、仓储物流)等各环节的过程相结合,然后在软件层面定义硬件,让合适的硬件发挥效率、创造价值。企业要有完善的流程制度如生产管理流程、质量控制流程等,再将这些流程融合到软件中,打造一个可执行、可操作的软件。
花金荣继续道,企业要有明确的诉求,这些诉求精确到每个部门、每个环节,然后通过对这些诉求的满足,从而打造一套可执行的系统,这才能够发挥软硬件最大的价值。因此,企业对自身诉求是否清晰,是否可以准确转达给合作企业,才是决定数字化、信息化转型成功与否的关键,而不是只是将责任归咎于ERP或者其他系统和硬件。“换句话说,企业在达到这样的境界之后,只要选择的合作方可以提供符合需求且可靠稳定的系统和产品,也基本上都可以保证战略上的成功。”
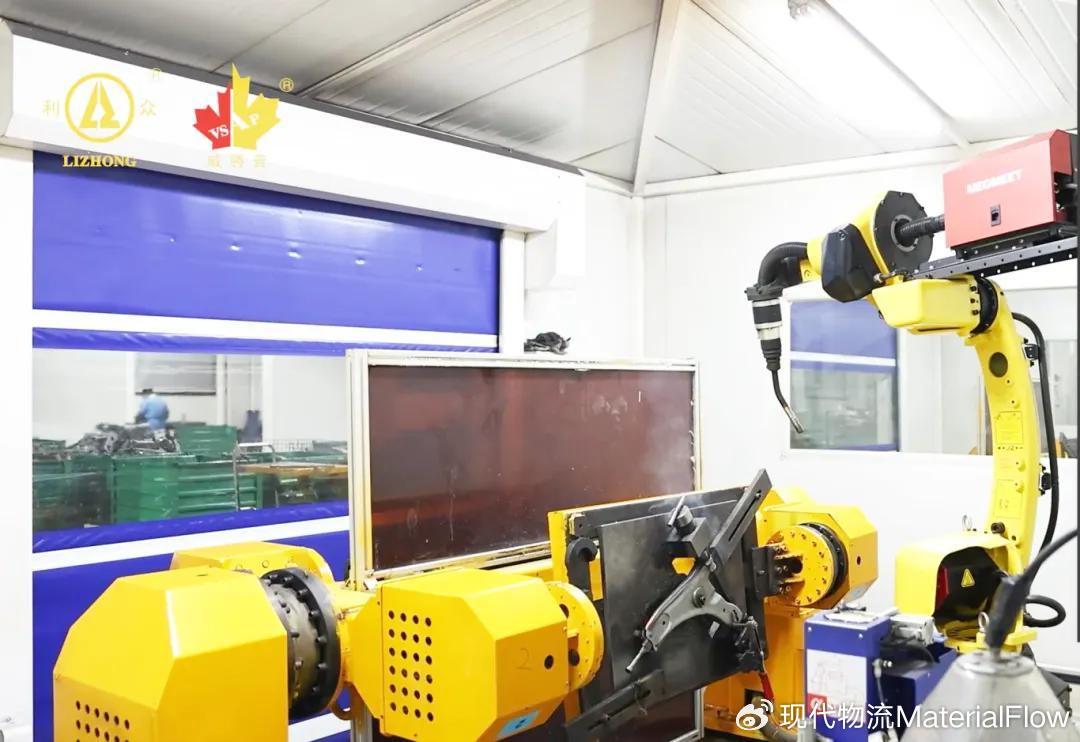
深入一线才能明确诉求
如何获取这些明确的诉求,花金荣也给出了自己的建议——即深入一线现场,以使用者的视角来审视每个环节面临的问题,并提出可行的解决方案,在不断地对细节进行梳理之下,取得处于不同层级的管理者和作业者的认可。“管理是从上至下,但数字化、信息化却需要反其道而行之,是要以基层为基础进行量身打造,而不是让基层削足适履,最终导致全盘的失败。”
04
推进国内外工厂智能化升级
当然,不仅是在中国国内工厂,利中底盘件也在泰国工厂积极地推进优化和升级改造。花金荣表示,因为主要客户市场都分布于海外,因此选择在海外建立工厂也是出于企业自身发展战略的需求,而且利中底盘件秉持了“本土化”的理念,在海外工厂几乎都以当地员工为核心建立了团队。据了解,泰国工厂已经完成了信息化的建设,并且也在跟随中国国内的步伐将管理的颗粒度提升到了小时级别的计划管理,保障了未来系统走向更精细化、更畅通的管理。
这些投入也包括了对于智能物流系统的建设。此前报道的利中底盘件位于玉环的工厂内,上线的智能物流中心高效地支撑了生产节拍的需求。对此,花金荣补充道,目前利中底盘件的零部件所需要的货位达到了8万多个,同时还要支撑产线小时级别的计划管理,因此无论是对仓储的密度、拣选的效率都提出了极高的要求,这已非人力能及,因此此前上线的智能物流项目也成了企业数字化、信息化的关键支撑。在此基础上,利中底盘件也将对泰国工厂的物料管理进行更多的投入,使其走向系统化和平台化,目前已经进入到测试过程中,完全上线后也将进一步提升仓储物流的作业效率。
采访最后,花金荣再度表示,从利中底盘件自身的发展过程来看,一方面数字化、信息化的转型升级不是一蹴而就也不是一劳永逸,另一方面决定企业在此方面的成败之处在于企业对于流程的理解和梳理,而不在于启用了相关系统和智能装备。也正是基于这样的理念,利中底盘件在未来仍将不断地推进升级和优化,从而适应“乌卡时代”实现更长久更稳健的经营。
END
《现代物流》| 文章精选
引领产业发展,成为世界级专业供应链物流媒体
本文版权归中国《现代物流》杂志所有,欢迎文末分享、点赞、在看!转载请联系后台。