智造发展需由点到面,共同拥抱数智化潮流。灯塔工厂被誉为“世界上最先进的工厂”,代表当今全球制造业领域智能制造和数字化最高水平。此次我们特别策划了“灯塔工厂”的系列报道选题,通过分析这些头部制造业案例希冀为读者提供一些智能制造的新视角。
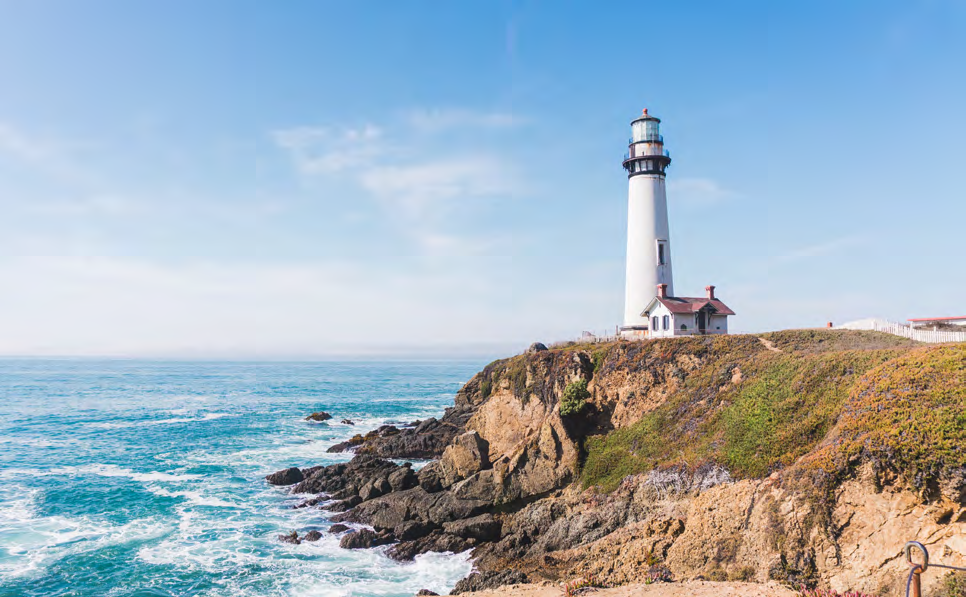
“灯塔工厂”充分运用自动化、工业物联网(IIoT)、数字化、大数据、5G等数字技术,应用规模处于世界最前沿,在业务流程、管理系统、工业互联网应用等方面广泛创新,为大家展示了驱动全球经济增长的最新生产方法。它是世界经济论坛(WEF)和麦肯锡咨询公司从全球众多家制造企业中共同遴选的“最先进的工厂”。
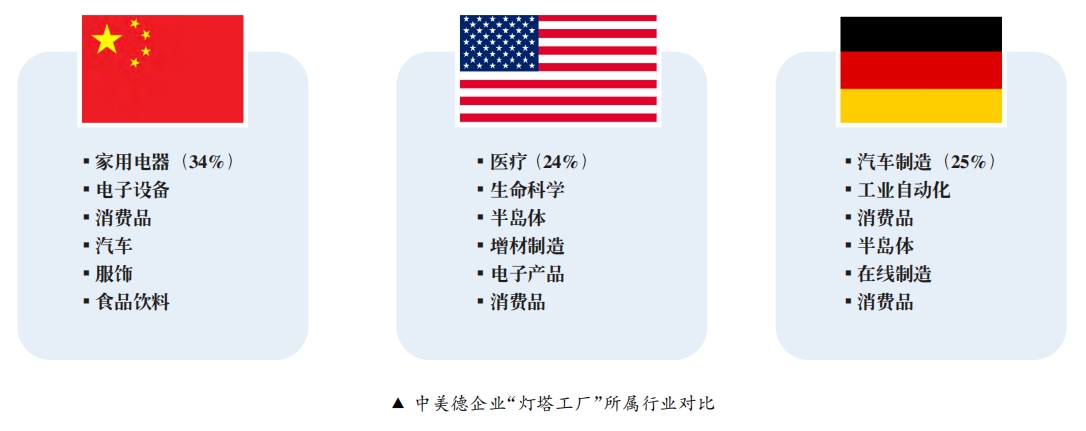
截至2023年1月13日,全球共有132家工厂入选灯塔工厂,分属于76家公司。从灯塔工厂所属公司所在国家的分布来看,排名前三的是中国、美国、德国,分别占比26.3%、25%、10.5%。其中,中国灯塔工厂数量远超其他国家,处于领先位置,这不仅表示中国正在积极应用关键技术推动转型,也将为市场带来大量新的机会。
从所属行业分布而言,覆盖了电子设备、汽车、消费品、家用电器、制药、服饰、食品等20余个领域。以工厂所属企业的国别而言,美国、德国的“灯塔工厂”集中于医疗、半导体、工业设备等尖端制造行业,中国的“灯塔工厂”主要分布在家电、电子等贴近终端消费者的离散型制造行业。
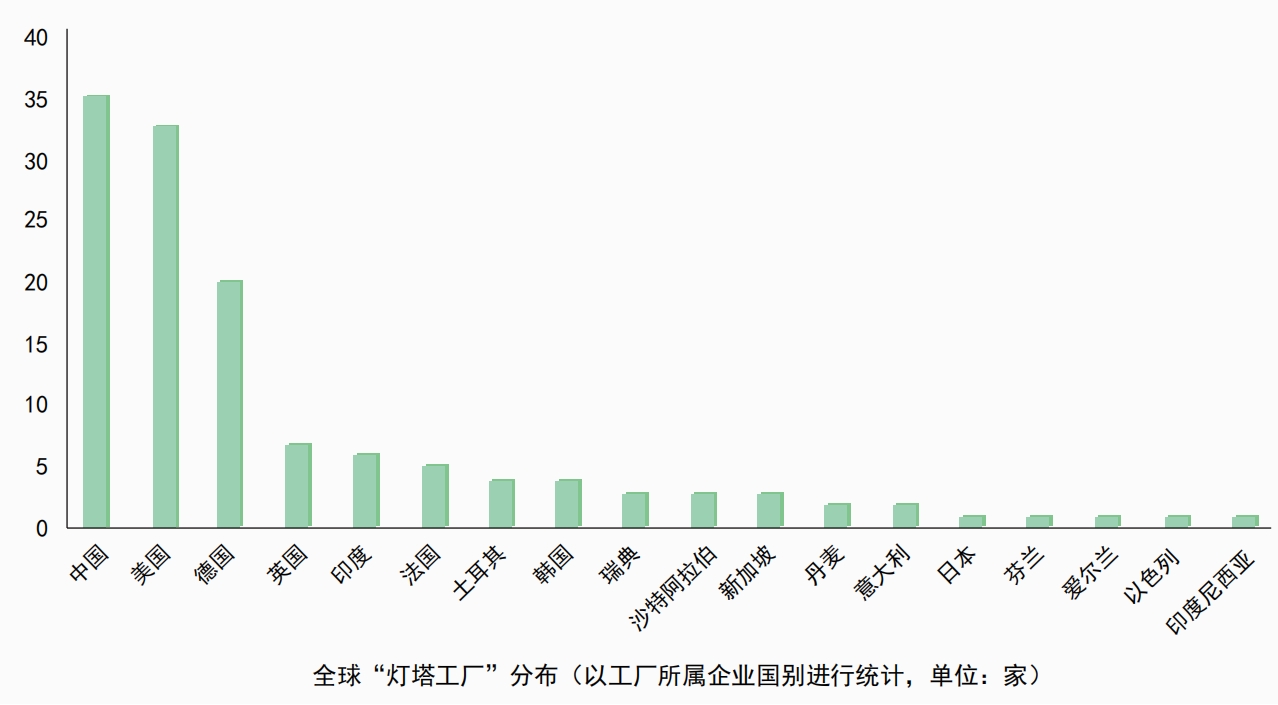
此前,我们已列举了几家大型企业的标杆工厂,以通过这些智能制造的探索经验,启迪更多后行者。在企业转型升级如火如荼的今天,越来越多行业正在深度融合数字化、系统集成和互联网等技术,提高业务运营管理。此次我们以工业设备为主题,了解该行业引领数字化制造能力的优势,并发掘企业实现灯塔工厂的潜力。
施耐德电气:美国莱克星顿工厂
施耐德电气是一家起源于欧洲的跨国企业,在秉承企业传统的前提下,进行无处不在的创新,以确保“Life Is On”的企业宗旨。为了保持业务和技术优势,施耐德电气美国莱克星顿工厂采用了革命技术,于2020年入选第五批世界“灯塔工厂”。
作为已建工厂的创新典范,莱克星顿工厂通过集成施耐德电气基于IIoT的EcoStruxure解决方案及其提供的增强现实、远程监控和预测性维护等最新数字化工具,实现了能效与可持续性总体的提高,并节约了大量成本。
具体而言,莱克星顿工厂部署了数字化能源管理战略,采用工业物联网连接和云预测分析来提高运营效率。在产品层面,EcoStruxure电能管理系统充分利用各种互联的仪表和传感器,进一步强化机器设备和流程的可视化效果和描述性分析。EcoStruxure Resource Advisor则可以提取详细的工厂数据信息,并部署能源管理平台,对能源成本和能源消费模式进行预测,帮助用户优化成本。
施耐德电气北美地区首席执行官表示:“施耐德电气证实IIoT解决方案有助于企业提高利润,并实现可持续发展目标。此次莱克星顿工厂跻身全球灯塔工厂榜单,促使我们进一步分享自身掌握的知识,助力企业提升可持续性和韧性,实现蓬勃发展。”
实际上,自2012年以来,莱克星顿工厂便开始对能源使用情况进行监测和分析,每年实现3.4%的节能率,累计节省了660万美元;智能配电(EcoStruxure Power)和智能楼宇(EcoStruxure Building)解决方案减少了26%的能耗和78%的二氧化碳排放量。
基于此,施耐德电气全球供应链被Gartner评选为“2020年度最佳商业赢家(Business Win of the Year)”,并凭借智慧物流获得“年度供应链突破大奖(Supply Chain Breakthrough of the Year)”。
博世集团:无锡工厂
作为最早践行工业4.0的工厂之一,博世全面部署并实施数字化转型战略,在制造及物流领域积极推进各类工业4.0应用,如实时的生产节拍时间管理系统、生产现场无纸化操作平台、智能仓储及物料管理等。其中,博世无锡工厂早在2018年就被评选为第一批世界级“灯塔工厂”。
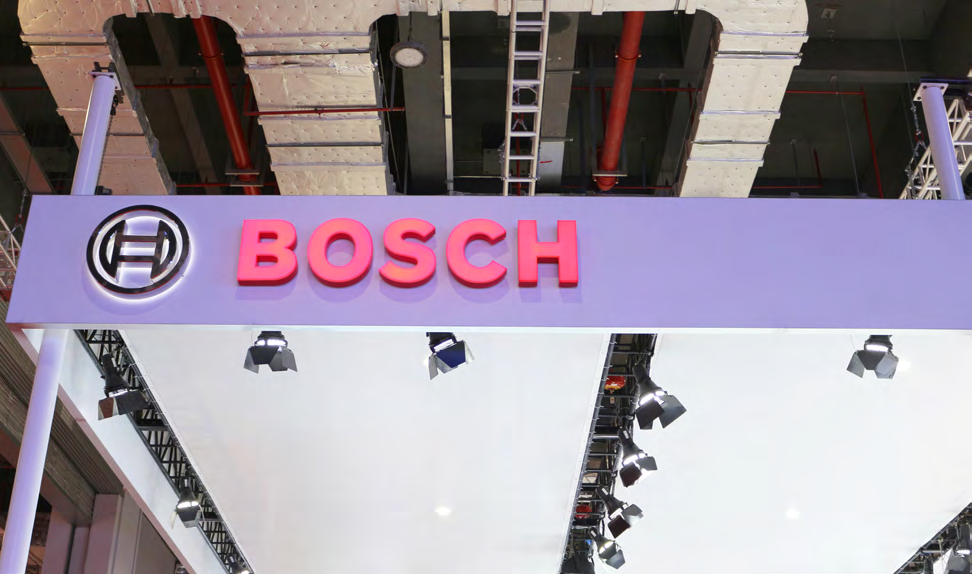
无锡工厂既是博世与智能交通技术在中国发展的重要基地,也是博世柴油系统和动力总成业务的中国总部。该工厂使用阀座人工智能自动目检台,实现了对复杂零件的自动上下料和快速对焦,能够对微米级别的失效尺寸进行连续拍照。这种快速对焦系统解决方案有效降低了30%节拍,显著提升生产效率。同时,高性能人工智能算法保证不同类型检测质量的准确性和一致性,使不合格零件检出率达到100%。
博世无锡工厂制定了全面升级的战略路线图,包括覆盖整个价值链的40多个项目。例如通过多个应用实例实现条件监测,使用智能系统优化设备能源消耗方案;应用RFID技术进行备件跟踪;通过数据分析不同场合的负载均衡和动态瓶颈等。
此外,该工厂自研的数据分析系统也是博世数字化转型的一大创新,整套系统涉及包含200多台机器的四条价值链,显著提高工厂生产效率。在新能源领域,博世的商用车电动化业务已全面铺开,率先在无锡建设了首个德国以外的燃料电池中心。据悉,这些燃料电池已在无锡实现批量量产。博世关注端到端价值链,用数字化转型提升整个产业链效能,促使新的业务模式和商业模式诞生。
构建数字化生态
实际上,灯塔工厂的数字化正在超出实体工厂范畴。2020年,博世中国创新与软件开发中心也于无锡正式落成,这是博世首个在中国开设的软件开发中心,开发包括嵌入式软件、云端和物联网解决方案、人工智能和大数据等,服务智能互联交通、出行服务、互联工业和智能家居等领域,预计到2025年将达到2,000人的业务规模,进一步服助力中国产业和技术发展。
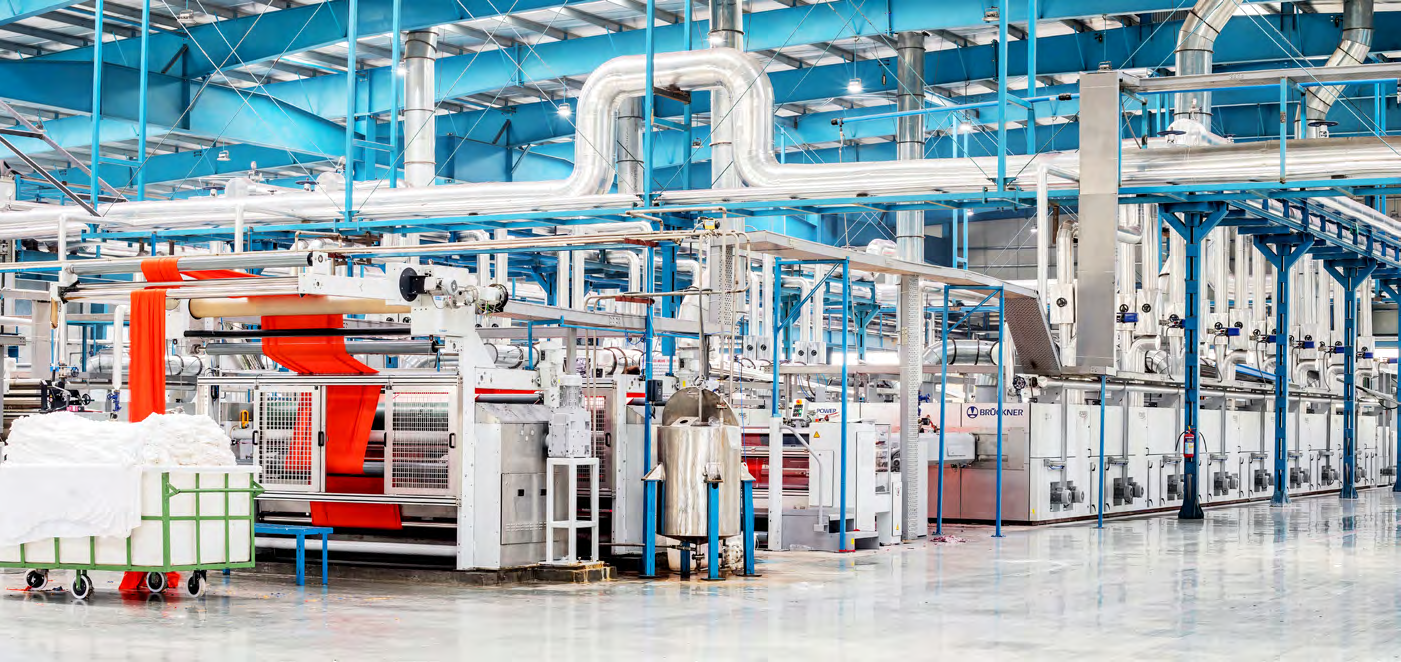
友达光电:台中工厂
友达光电成立于1996年,旗下涵盖显示科技、系统解决方案、智能制造、医疗照护与绿色能源等事业领域。总部位于中国台湾,是全球第三大液晶显示面板制造商,拥有从G3.5到G8.5的完整世代线,营运据点遍及亚洲、美国与欧洲,目前全球员工约38,000人。2022年合并营业额为新台币2,467.9亿元(约565.15亿元人民币)。
友达光电为全球首家承诺于2050年全面使用再生能源的显示器制造企业,其台中工厂于2021年获全球灯塔工厂,在当时评鉴为“大数据与AI技术开发与广泛应用,展现工业4.0自驱动的永续发展动能。”实际上,友达光电台中工厂项目亦是全球第一个获得LEED金级认证的光电面板工厂。
在数字化转型背景下,友达光电台中工厂以显示技术为核心,整合软硬件、云端与服务平台,共筑智能物联生态圈。该工厂自2015年启动智慧制造,从规模竞争转向价值竞争,通过应用AIoT数字化、资料科学技术,开发智能水电网系统Smart Grid。该系统实现友达光电台中工厂在2018至2020三年间减少23%的用水量、20%的碳排放量,以及6.4%的电力消耗。
与此同时,友达光电台中工厂在内部启动组织转型,在智能制造、绿色供应链和人才培育三方面进行优化,将生产成本降低15%,并提升生产效率至30%以上。友达光电台中工厂的节能减排、降本增益成效明显,其发展思路也为其他制造企业的转型升级提供了参考借鉴。据报道,友达光电将于台中加码投资千亿元新台币扩建厂房,兴建8.5代线级新厂,预计2025年投产。
总之,制造企业是伴随着精益生产和质量管理体系而发展起来的。其“灯塔工厂”的价值链目标通常为——生产定制化程度高的创新产品,由于产品创新程度与消费者需求程度较高,转型升级的重点是价值链的数字化重构,如上述文中提到的施耐德电气美国莱克星顿工厂、博世集团无锡工厂、友达光电台中工厂。因此,灯塔工厂基本通过采用数字维护、数字管理、可持续发展等举措。构建覆盖企业内部全流程、产业链上下游全环节、产品服务全生命周期的数字化体系,提升企业及产业链效率、降低成本;同时通过数据要素探索新的模式,以形成新的增长点。
(未完待续……)
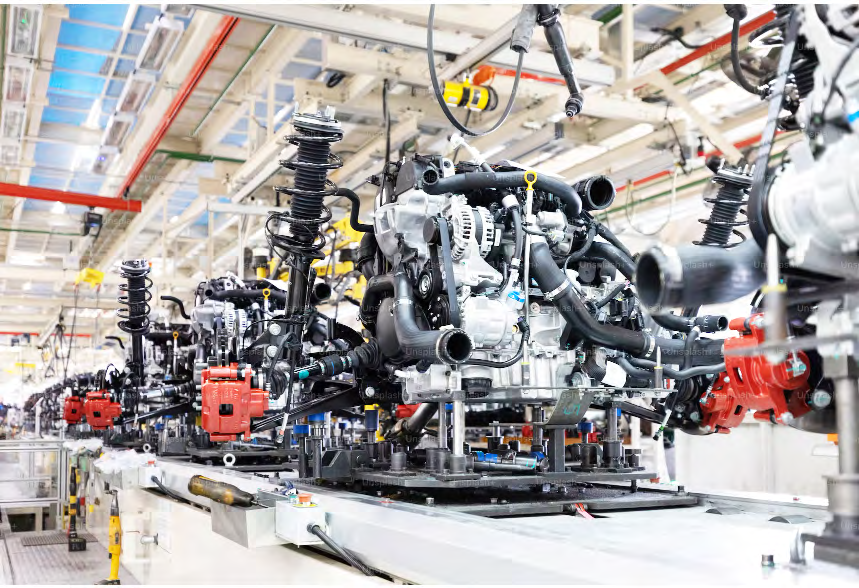