——专访广汽丰田有限公司总装一部总装技术1科科长 钟裕民
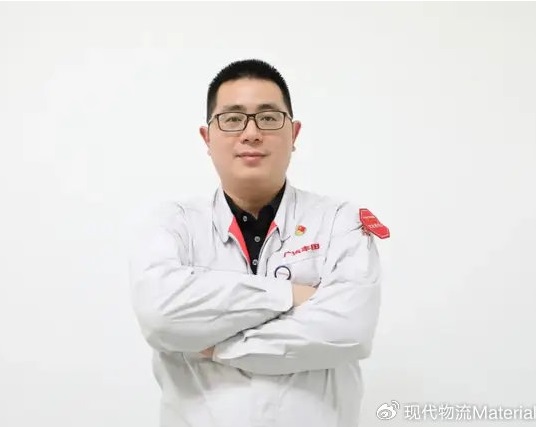
广汽丰田有限公司总装一部总装技术1科科长 钟裕民
企业介绍
广汽丰田汽车有限公司(全文简称:广汽丰田)成立于2004年9月1日,是由广州汽车集团股份有限公司和丰田汽车公司各出资50%组建的合资企业。广汽丰田扎根广州南沙,具有粤港澳大湾区核心区位优势。持续改善创新,始终保持稳健的高质量发展态势,被誉为21世纪丰田全球模范工厂。
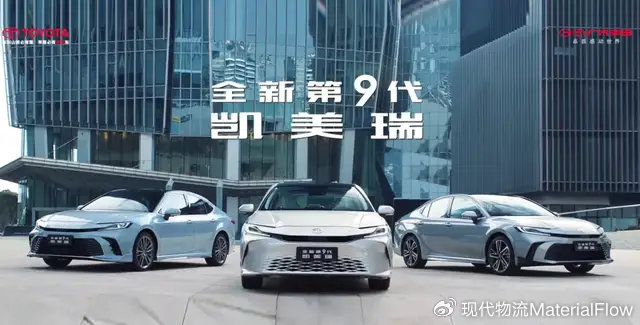
精益生产历经多年的发展,已超越了单纯的生产方式,成为一种先进的管理理念。汲取丰田精益管理的精髓,广汽丰田的精益模式在中国的实践已走过二十多个春秋,其发展路径也在持续地优化与升级。在当今智能化浪潮的推动下,广汽丰田与华章智能携手合作,成功实现了多层穿梭车在动态汽车生产线上的首次应用。
PART.01
基于精益理念 不断探索数智化新发展
丰田是全球领先的汽车制造商之一,其生产工艺和智能化优势在全球汽车行业享有盛誉。其中“丰田生产方式”(Toyota Production System,TPS)旨在消除浪费、提高生产效率和质量管理。而TPS的核心理念主要涵盖了Just In Time(JIT)和平准化管理体系,共同构成了精益物流供应体系的基础,如今亦被各行各业的管理者们认可与采纳。
广汽丰田作为丰田全球的模范工厂,继承了丰田数十年来汽车制造的精髓,自2004年成立以来,便以精益理念为核心,围绕TPS、JIT和平准化原则,并引进了全球最先进的生产设备与工艺技术,在全球首次导入了全面的SPS模式(零部件分拣系统),实现了部品的选取和装配的分离,极大地提升了生产效率和品质。构建了首条SPS模式(丰田物流分装生产线),不断提升装配效率和质量。
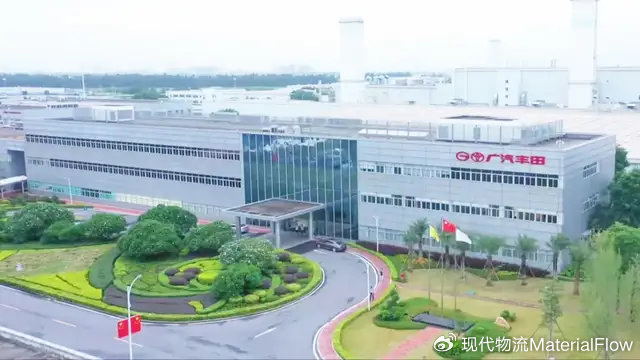
TPS的核心特点之一是以最终用户的需求为生产起点,以拉动式生产模式实现作业流程最短化和库存的最少化,因此广汽丰田注重物流平衡,致力于实现零库存。它要求企业实时反馈订货信息,从而促进生产与销售环节的并行化运作,通过消除生产中的一切浪费来达到综合降低成本的目标。
广汽丰田伴随着技术的进步不断对这一理念进行优化,形成了当前的智能化高效物流系统。目前,广汽丰田拥有5条生产线,年产能约为100万台,能够同时生产超过十种不同车型,是丰田在全球范围内规模化和集中化程度最高的生产基地之一,且生产线的效率已达到每58秒下线一辆车的惊人速度。主要销售车型包括凯美瑞、汉兰达、威兰达、雷凌和塞纳等,其2024年工业总产值有望达到1,500亿元人民币。
广汽丰田总装一部总装技术1科科长钟裕民表示,“我们运用了大数据、数字化、物联网等先进技术,构建了供应商、广汽丰田与顾客三位一体的智慧供应链体系,实现了低成本、短周期的零库存柔性生产。广汽丰田致力于为顾客提供高价值的产品、高品质的服务以及高品位的体验,并将‘一切为了您的微笑’作为我们的企业使命。”
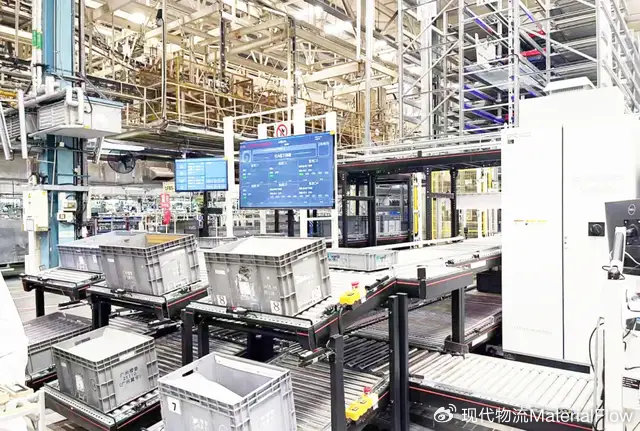
随着中国物流领域不断发展,广汽丰田为积极应对中国市场变化,加深对智能化的理解与实践,持续提升自身的综合实力。在生产与物流管理过程中,结合IoT技术,广泛采用机器人、无人运搬车等智能制造与智慧物流技术,不断改进制造工艺和物流管理模式,提高生产效率和物流质量,降低企业成本,继续引领汽车行业的发展。
PART.02
JIT技术背景下的柔性挑战
广汽丰田针对当前物流环境,构建了适应本地需求的物流体系。鉴于中国物流行业的迅猛发展和科技飞速进步,广汽丰田深入考虑了中国国内的先进技术以及零部件仓储企业的实践经验。结合丰田的核心理念,广汽丰田进行了深入的本土化开发。
钟裕民指出,与其他行业设立固定的仓储中心不同,广汽丰田在工厂内部实施了进度管控,从而形成了一个流动性更高的无仓储管理体系。此外,丰田的SPS系统在管理上与其他行业存在显著差异。在广汽丰田的生产模式中,平准化概念得到了应用,并通过看板管理实现了先进先出的原则。在考虑仓储概念时,广汽丰田会遵循丰田的七大浪费原则,认为仓储本质上是一种浪费。因此,如何根据这些原则消除浪费,并利用新技术来优化作业流程,正是广汽丰田所面临的挑战。
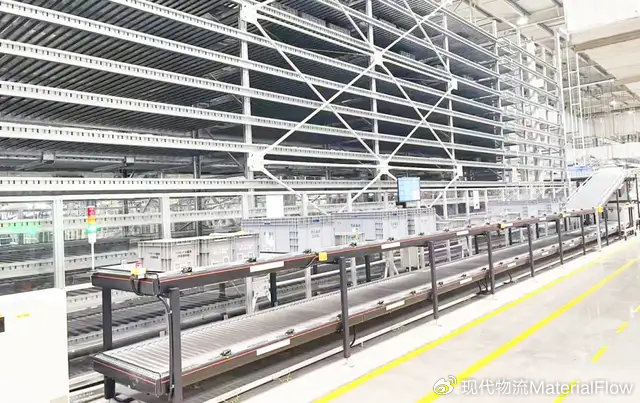
以穿梭车技术升级柔性产线
广汽丰田的内部物流流程涵盖了从P链或PC区到SPS以及生产线的各个环节。鉴于此,在推进创新改革的过程中,广汽丰田根据当前的生产状况,寻求适宜的技术解决方案,以实现更高层次的科技创新。特别是在SPS拣货区域,传统的人力循环拣货方式导致了部品选取作业的效率低下。
针对这一问题,钟裕民在一次行业展会上接触到了多层穿梭车技术,并认识到其高效和灵活性的双重优势。相较于传统的堆垛机,多层穿梭车的起货效率更高,能够适应丰田每58秒下线一辆车的生产节奏。同时,广汽丰田的工厂内部实现了多车型的柔性生产,单条生产线的日吞吐量超过6万箱,因此面对着繁多的SKU品种和复杂多样的包装容器。穿梭车技术的灵活调节功能正好能够应对这些挑战。“基于这两个原则,我们开始探索如何将这种新技术与汽车生产流程中的各个环节相结合,并评估其应用的可行性。”
动态实施的需求
SPS作为一种向生产线提供单台份成套零部件的配送方式,有效解决了从“一托”货物到“一箱”货物单位的转变。然而,一旦货物进入生产线,就需要按照单个单位进行流转。广汽丰田期望通过引入穿梭车技术,实现SPS供应流程中“一托”“一箱”与“一个”货物存储单位之间的高效转换,满足了生产线末端快速的需求。
钟裕民强调道,“我们的整个生产链条非常敏感,任何异常都可能导致末端生产停滞。因此,动态实施过程对效率和准确度的要求极高。基于此,我们在项目需求上主要聚焦于实现高效、低成本和高精确度的三重目标。”
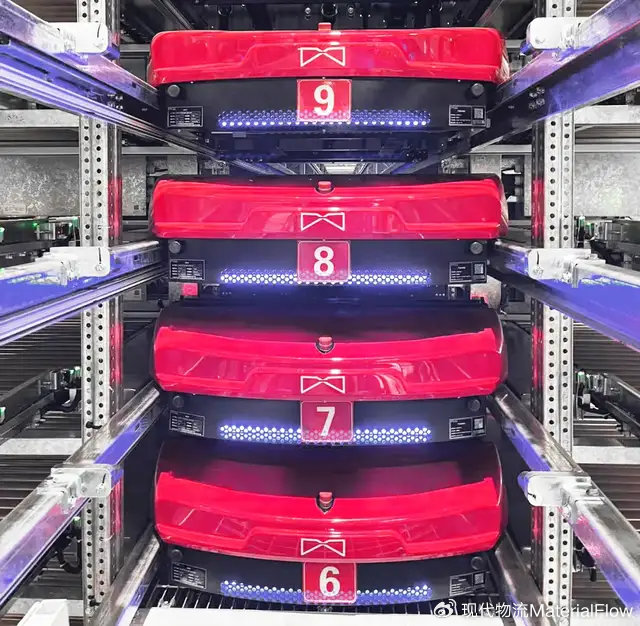
自2024年夏季起,广汽丰田开始内部探讨,旨在通过多层穿梭车的拆零拣选方式,并结合丰田的TPS理念与SPS的投入方式,制定一个既符合实际生产需求又高效的解决方案。实际上,穿梭车技术以往多应用于传统仓储项目,主要作为仓储的功能,流通性低,而将其融入整车制造的生产环节,实现动态的高效流通,这在技术应用上尚属于首次尝试。
PART.03
携手华章智能 打造高效智能物流体系
丰田的物流订单与生产线分别由两个独立的系统进行管理。因此,解决方案需要一方面与外部物流系统相结合以实现订单的入库,另一方面则需与生产线的柔性生产系统相融合。基于这样的需求,华章智能在深入研究丰田的生产方式后,为整个仓库管理系统和拣货系统开发了一套全新的系统。
“作为高速穿梭车领域的领导者,华章智能的产品效率在中国国内名列前茅,其团队的专业性也极为突出。在实际案例考察中,我们发现华章智能的技术成熟度和产品稳定性都极为出色。在全面评估了华章智能的技术实力、行业定位、定制化服务能力以及管理协调能力后,我们最终决定选择华章智能作为项目的合作伙伴。”钟裕民在选择华章智能作为合作伙伴时所依据的考量标准。
项目亮点彰显技术优势
据悉,该项目占地面积约300平方米,高度约6米,共14层,设有12个拣货口,可实现两侧同时进行拣货作业。该项目的优势主要体现在以下三个方面。
首先,华章智能为广汽丰田的立库设计了回型线体,使货物能够快速完成拣选和回库任务。同时,设置了捡货指示系统,通过亮灯的模式帮助员工迅速对拣选货物进行顺序匹配,从而提高齐套配送产线的效率。
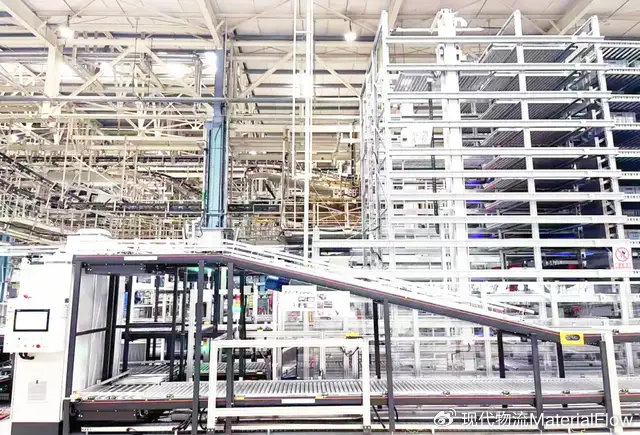
其次,华章智能在立库每层均安装了一台高速穿梭车,并通过配置双侧提升机,在更小的占地面积内实现了更高的效率。值得一提的是,其单巷道可处理高达1,336箱/小时的流量。
此外,为满足客户需求,华章智能设计了多箱型混合存储方案,并定制了可变式货叉,以适应不同尺寸的箱体(最大尺寸为800*600,最小尺寸为340*280)。这一设计进一步节约了存储空间,提高了企业的存储密度,并增强了流程的灵活性。
在软件开发方面,鉴于丰田生产系统与外部生产系统存在差异,它要求按照特定序列进行单件生产,这要求出货也必须遵循相同的顺序。华章智能在与客户多次现场沟通后,特别定制开发了软件,采用严格的排序方法来解决序列管理的难题。
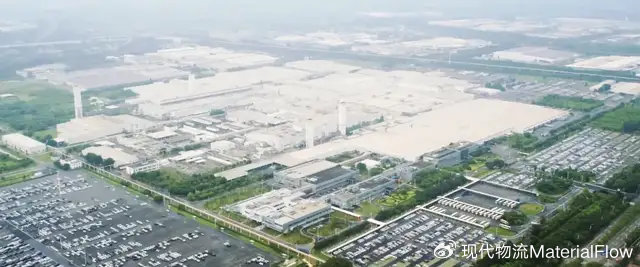
“在软件的定制化开发方面,华章智能的工程师展现了极高的配合度。他们能够迅速根据我们的需求提供反馈,并在实际运行测试中不断识别并解决新出现的问题。”钟裕民对华章智能的服务效率和响应速度给予了高度评价。
此外,广汽丰田的电气安全标准与中国国内安全体系有所不同,它比行业通用标准更为严苛,实际上是一个全球范围内较为独立的安全标准。因此,在项目实施过程中,华章智能面临了多种安全标准的兼容挑战,并进行了长时间的策略调整,以确保满足广汽丰田的安全要求。
技术革新下效率翻倍
从“一箱”到“一个”,广汽丰田在首次引入立库自动化技术取代传统的人力拣选之后,实现了高效率、高精度的物流运搬和零件拣货,既符合丰田TPS的生产理念,整体运行效果也达到预期目标,其中拣货效率翻了一番,物流运转效率则提高了约70%。
“我们与华章智能的合作也是对丰田物流体系进行现代化升级的一部分,通过引进中国国内的先进技术,不断进行创新应用,以实现丰田物流模式在中国的本土化革新。”钟裕民最后说道。
END
《现代物流》| 文章精选 133期
引领产业发展,成为世界级专业供应链物流媒体
本文版权归中国《现代物流》杂志所有,欢迎文末分享、点赞、在看!转载请联系后台。