自动搬运机器人开始在自动化的第二阶段中大显身手。
通过尖端科技与公司优势开拓“2030愿景”
以鸿池运输株式会社为核心的KONOIKE集团宣布了其“2030愿景”,也就是对2030年(公司成立150周年)的商业环境变化作出预测,以中期管理计划(2019年3月至2021年3月的财政年度)为基础,定下经营方向。同时,该公司宣布一系列举措,旨在通过将人工智能、机器人等新技术与公司多年发展优势相结合,开拓全新的服务市场。
KONOIKE集团还投资了一家专注于先进技术领域的风险投资公司(GTV FundI Investment,L.P.),以便通过技术创新加强物流现场的实践能力,并加速创建新型业务;并计划在改善工作环境、解决日益严重的劳动力短缺问题的同时,与世界各地的技术初创企业进行接触,以提高生产力和加强现场实战能力,并致力于发现和培育新的核心业务,进行价值创新。
分属于该公司关西中央分部的“西大阪配送中心”,是一处负责企业客户办公用品网购配送业务的物流基地。
关西中央分部西大阪配送中心的副经理森川邦彦介绍道:“从2004年6月,本中心开始承担网购部门的仓库运营工作,承包入库、保管、出库、包装、发货、退货等一条龙服务。西大阪配送中心于2016年9月正式投入运营,总建筑面积为48,190平方米,建筑共高四层,配有一系列自动化物料处理(MH)设备,传送带总长度超过3,600米,也是本公司最大的配送中心。”
西大阪配送中心概况
西大阪配送中心的建筑结构共分为四层(图表1),一层除出库区之外,主要负责处理大批量运输的日用品和饮料等货品,并对中心的日常出库工作快速进行处理;二层用于储存和运输制造商所包装的大件商品;三层有一个收货区,负责对入库货品进行检查并送至各楼层,同时也会进行特殊商品和大件物品的存储和出库;四层则是处理各种小批量的办公用品和日用品,并完成各种货品出库。
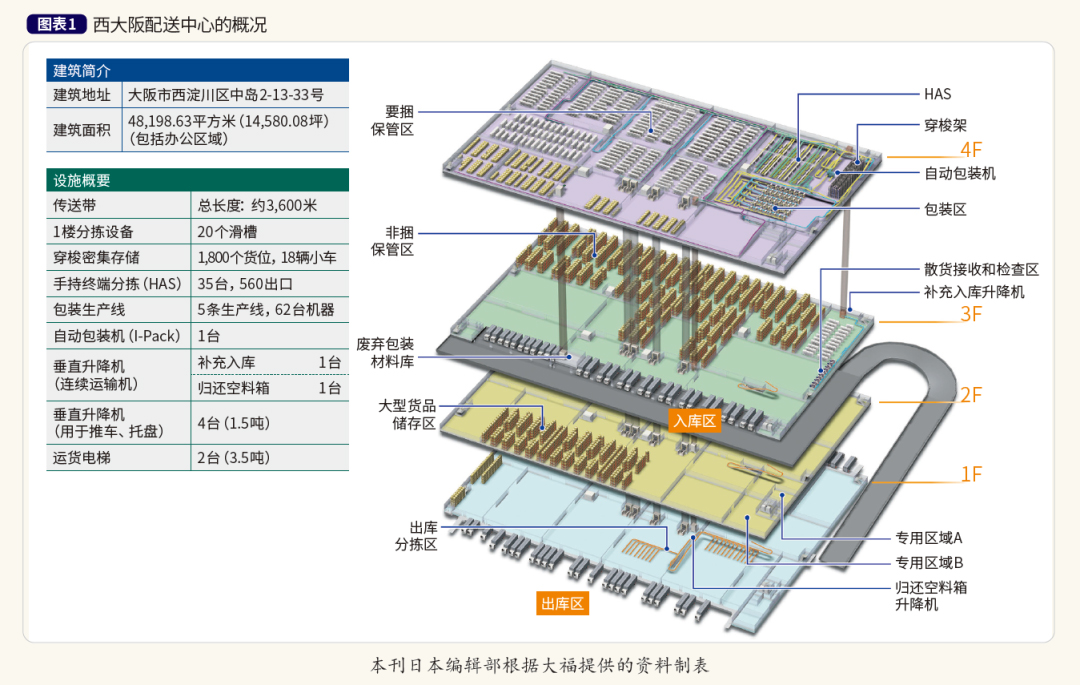
让我们大致概览一下货品在中心的流动情况吧。
货品运到三层入库区后,司机使用手推地牛进行卸货。工作人员对货品进行查验后,根据特性把货品送到相应的储存区。不适合装入料箱的货品,如长条形货品,统一汇总到异形包装货品区,并存放至该层直接进行包装运输。
送到各楼层的货品会被各自运送到指定货架进行存放。前三层使用叉车,第四层则使用手推地牛。出库频率高的货品会以托盘的形式存放到货架上。
森川先生表示,“公司会分情况使用自有物流和快递进行送货。针对包含大阪在内的近郊地区会使用当日达的自有物流,每日上午和下午分别配送两次;其他地区则使用次日达的快递。”
耗费两年完善构思
该中心经营的商品基本都是面向办公室的B2B物流,拥有数以万计SKU。这些业务包含当日达和次日达,每天需要对数万件订单迅速做出反应,很难同时兼顾商品的准确存储、拣选、分类等作业的质量和生产效率。
该中心的运营领导人宫本惠示所长谈及企业目标时说道:“我们的目标不仅是实现自动化,还要充分发挥机器和人各自擅长的能力,制定运营规范。不论是仓库布局设计,还是MH设备的选择,都按照该方针进行。开业之前,货品曾存放在旧物流中心和两个外部仓库,共三个地点,总共占地约9,000坪(29,700平方米),为了将三处仓库进行整合、提高效率,我们规划了这处新的物流中心。为了利用这处单层足有5,000坪(16,500平方米)的区域,我们与合作伙伴一同,对拣选方式等仓储问题进行无数次讨论。大概花费两年时间构建全新的工作流程、设备配置和布局。”
第一年的主要工作是让现场的所有成员聚集在一起,找出所有现存问题。在第二年,公司和自动化MH设备供应商大福一起讨论了工作流程、库内布局和拣选方法,建立一套独有系统。据说当时中心为了讨论并解决各种问题,各相关方每周都要聚在一起进行2~3个小时的讨论。
“这里的设计从构思到建立,花了很长时间,但我认为这些努力没有白费,现如今,我们已经大大消除了传统现场所存在的问题。”宫本所长自豪地说。
森川邦彦先生
宮本惠示氏
以四种拣选方式推进合理化
在对新中心的构思之中,最显著的特征就是将主要的拣选方式从接力拣选切换为总量拣选。为此,中心引进了大福公司制造的穿梭货架(快速立体料箱分拣系统),大大提高了最终按客户分类,进行分拣工作的效率(图表2)。为了进一步应对种类繁多的产品出库,现在结合使用以下四种分拣方法:
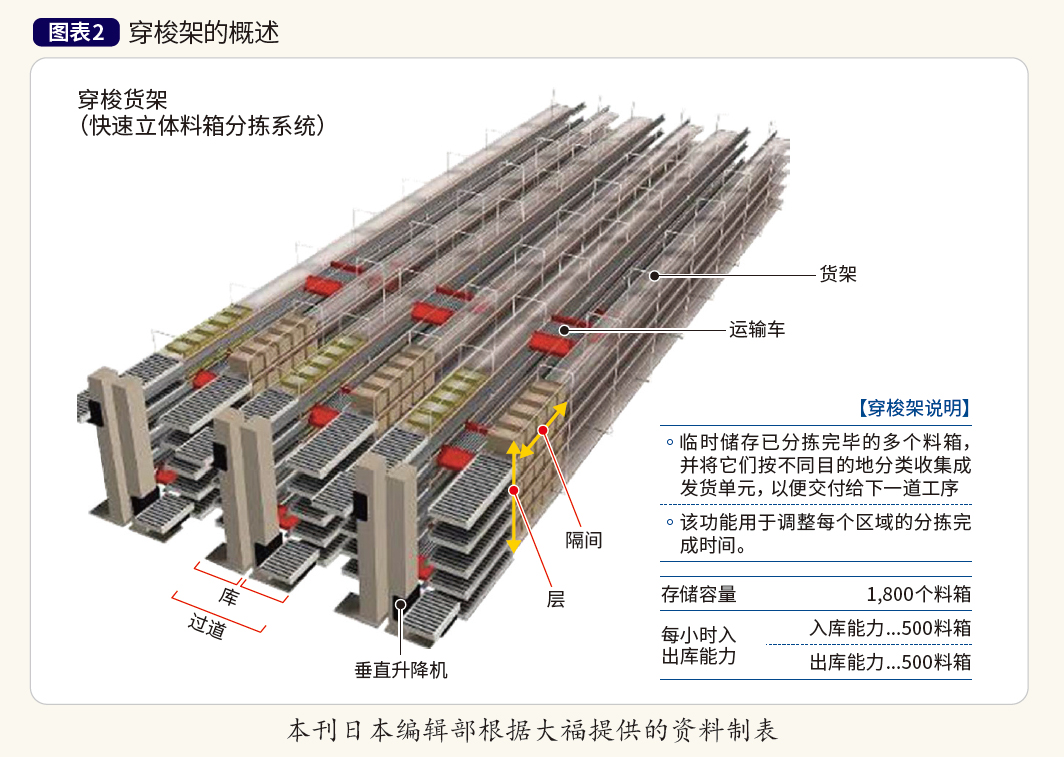
一是总量拣选方式,每个区域同时进行拣选,利用穿梭货架进行汇总,在下一道工序中进行分类。二是单行拣选方式,挑选出各个区域中单一货品订单,依靠推车进行拣选,不使用传送带。三是区域内订单拣选方式,在每个区域中挑选出能在区域内完成的多种商品订单,拣选完成后,通过分流线把订单直接送到包装区域。四是成箱拣选方式,挑选出以箱为单位的订单,依靠推车进行拣选,不使用传送带。
将主要的拣选方式改为总量拣选的原因是,旧物流中心采取的方式曾是接力拣选,但在实践中出遇到了各种故障问题,令工作负荷大大提高。
传统的物流中心采用的接力拣选方式,即以订单为单位,依次拣选各个区域的商品。其缺点也为众人所知,如果每个区域都有多重商品订单,则会发生重叠的拣选路径,导致工人步行距离增加,并且需等待下一个拣货周转料箱的到达,增加了工人的等待时间。为了解决这些问题,该中心决定进行更改为整体拣选方式。
经过深思熟虑后,中心采用的工作流程是:在每个区域将16个订单分为一个批次,把订单中的货品一齐拣选出来,再按物品类型分类放入折叠货箱(以下简称料箱)。然后,将料箱送到装卸区的穿梭货架上,并临时存放。从这里集中出库已完成集货的同批次订单料箱。
下一道工序是HAS(手持终端分类系统),工人使用手持终端将料箱中16个订单的货品按目的进行分类。在批量处理这些订单时,无论是拣选还是分类,都只需最短的步行距离。这样就可以随机应变地分配工人到订单较多的区域。采用总量拣选方式之后,中心拣选处理能力大大提高。
负责工作进度和设备管理的小组组长中村刚志先生讲述了物流中心改变拣选方式的另一个原因,“我们之所以决定采用总量拣选方式,也是考虑到入库作业的效率。新中心决定为每家客户划出存货的固定区域。这可以大大减少入库时的工作负担,也让总量拣选变得更有效率。新中心还采用了旧中心无法实现的想法,例如给大型商品划出专用区域,为以托盘为单位入库的货品划出托盘专用存放区域等。”
举个例子,中心四层使用了后文提到的自动搬运机器人(图表3所示)。这些区域依序编号为401到415,每个厂家都把货品存放在固定区域。在这12个区域中,目前除了408号区域之外,有11个区域正在进行拣选。
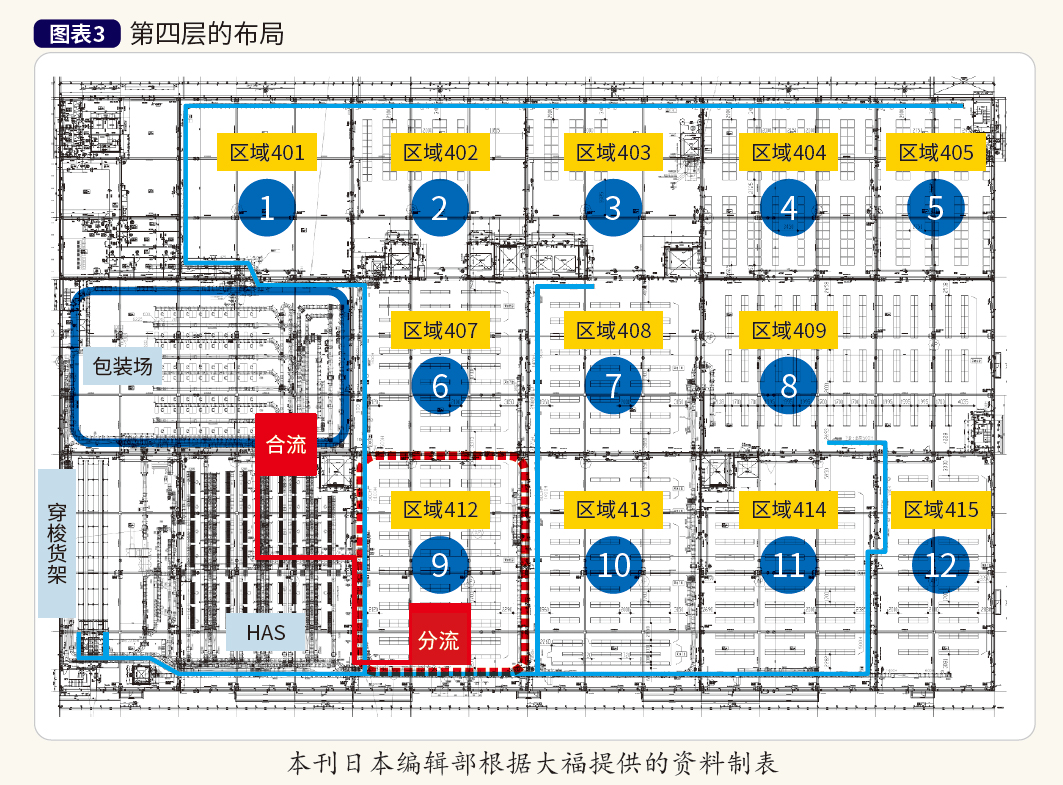
负责管理现场的主要领导松林龙太郎说,“举个例子,假如客户订购了圆珠笔,他不会分别给黑笔和红笔指定不同的厂商,因此这种情况下可以在同一个区域进行分拣。通过给各个厂商指定专属的库区,出库时商品也会沿着流程漂亮地送出去。”他指出,在库区中按制造商分类储存也有利于实现高效拣选。
“不管怎样先试试”
该中心转型为总量拣选之后,实现了物流合理化,但随着客户业务的增长,出货量逐年增加,传送带“堵车”现象也随之而来。因此,尽管通过挑选出各个区域中单一货品订单进行“单行拣选”,可以减轻机器负担,但仍无法解决传送带“堵车”问题。
面临这一情况,针对传送带“堵车”导致工人长时间等待,有人提出建立一条分流线的想法,即货品无需在拣选后进入穿梭架等待进一步分拣,而是直接运往包装场。因此“区域内订单拣选方式”应运而生。
这种方式,一开始就将单独区域的订单分出来,进行单独拣选,将货品放入料箱,通过分流线直接运送到包装场。在单独区域内完成的订单省去了穿梭货架的等待时间,在拣选时,它的送货地点就已确定。通过跳过穿梭货架和手持分拣系统的工序,减少工人的等待时间,并有效避免了料箱“堵车”。
“我认为,将可以在单独区域内完成拣选的订单挑选出来,利用其它手段进行拣选,然后通过分流线直接运送到包装场的这一方式,是前所未有的创新想法。我们每天都在作出类似努力,以弥补整体拣选的缺点。客户在一周内的不同时间和淡季旺季所产生的巨大需求波动,上下相差达1.5倍左右,单靠机器的能力是无法应付的。我们已开始重新审视流程本身,并且集思广益,考虑建立新的机制来克服这种波动。”宫本所长分析道。
同样,“整箱拣选”也是挑出以箱为单位的发货订单,并采用其它手段分开处理,为此该中心也采取了各种各样的巧思。
质量控制和教育负责人组长大野泰继补充道:“例如,我们会使用推车拣选,减少传送带的负荷,但为了让推车使用起来更快捷,我们又在推车上添加许多功能,例如轮子刹车器和制动器等。我们中心的特色是,任何在现场能想到的东西,都要先去试一试。”
就这样,中心管理人员相互交流智慧,每当新的挑战出现,他们都会进行各种改进,以更好发挥设备能力,实现脑海中设想的理想状态。
各种改进想法不仅来自中心管理部门,也来自在中心的日常工作人员。该中心的强大之处在于它不仅能够听取工人意见,而且能够迅速着手加以实施。因此,参观者经常会惊讶地说:“这里和上次来的时候完全不一样了。”
关于拣选方式改变后达成的效果,宫本所长说:“尽管总量拣选使拣选速度得以提高,但与此同时,穿梭货架和手持分拣系统的分拣工序也必不可少。所以我们没办法简单地比较效率,总体上而言,效率提高了约10%。现在工人不需要等待时间,可以同时作业,所以我认为我们的爆发力得到了确确实实的提高。”
中村刚志先生
松林龙太郎先生
应用自动搬运机器人
除了穿梭货架之外,该中心还采用了其他自动化设备。
其中之一就是将包装工序的自动化系统“I-Pack”投入使用。该系统具有自动测量装箱货品高度,将箱子调整到适当高度并密封的功能,目前的运行成绩相当于18名工人的工作量。这使得高效率的人员配置成为可能,例如可以将这些节约下来的人员分配到拣选工作中去。“I-Pack”使用的是一种专用纸箱,包装时该纸箱的高度可以根据内容进行调整。
然而,目前中心仍然有许多商品是手工打包。例如,公司自有物流负责配送附近的货物,公司自有物流的司机能够始终小心处理货品,所以货品只需手工用塑料袋进行简易包装即可。如上所述,该公司是根据客户的要求,来确定自动化处理货品。
另一处自动化设备则是在四层投入使用的两台自动搬运机器人。“OTTO100”和“OMRONLD系列”,都不需要磁带和其他引导路线,可以在中心内自动寻路,帮助工人进行存储和补货的搬运工作。挑战将机器人投入实际使用,鲜明地标志着公司的自动化工作进入了一个全新的阶段。
松林先生解释道:“大致而言,‘OTTO100’用于在附属办公室与作业现场之间交换货品及发票,而‘OMRONLD’则在不同区域间运送货品。图表4中的蓝线代表‘OTTO100’,绿线代表‘OMRONLD’的行驶路线,运输对象以当天入库的商品为主。这种自动化作业不仅节省了工人步行量和时间,还提高了附属工作的效率。”
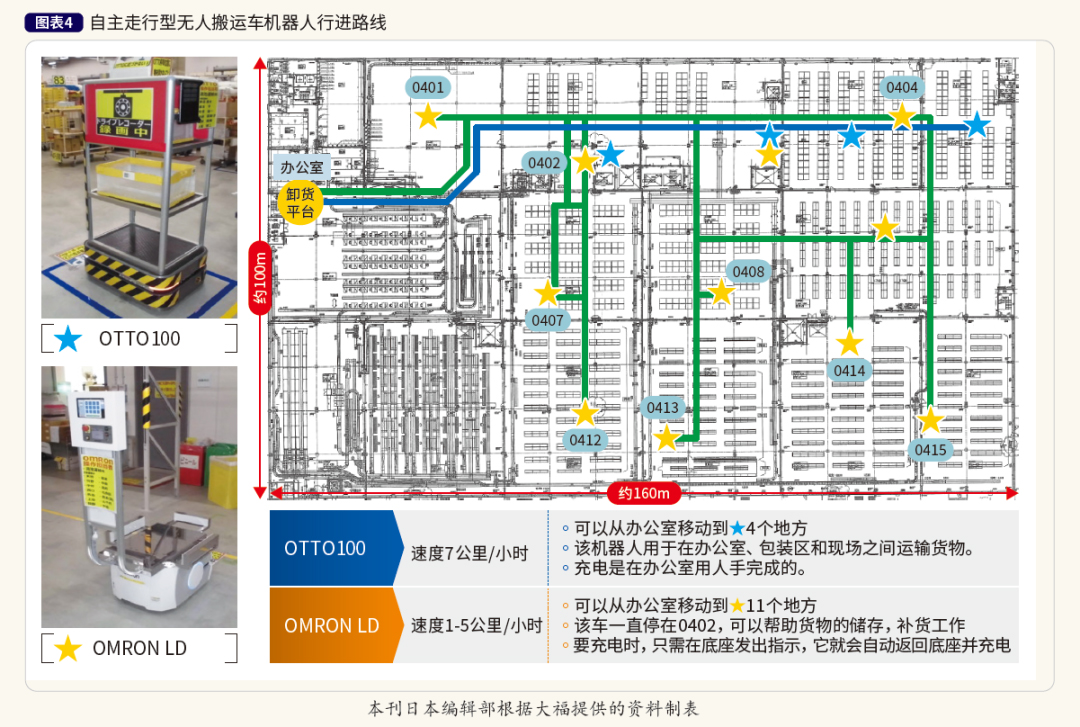
这里提到的附属工作之一,是用户坚持要求提前交付货品时所产生的临时措施。在这种情况下,工人必须拿着拣货单在每个货架上拣选货品,如果每天发生几次类似订单,就会产生相当长的步行距离。与其让工作人员往返取货,不如在每个区域准备好货品,工人把它放在机器人上运输,这样可以大大减少步行距离。
森川说:“运行路线有限制的‘OTTO100’每天会运行1公里左右,‘OMRON100’每天会运行3公里左右。”
第三层铺设了一条传送带,可以把入库货品自动运送到各个区域,除此之外,还有一些货品会连同托盘一起运到第四层,单靠传送带可能无法完全处理。据说,“OMRONLD”在减轻搬运工作上也发挥了作用。
“通过投入自动运输机器人,我们学到了很多,”宫本所长表示,“运输机器人最大的缺点是,如果入库货品太多,堵塞了通道,它们就跑不动了。尽管这些搬运机器人在制造业的工厂里大显身手,但在物流中心却一直没有得到广泛应用。使用之后发现,最重要的原因就是无法给它保证通道。在这方面,我认为本中心对通道的划分很清楚,所以搬运机器人仍拥有很大的应用空间。在目前的实验过程中,我们正在尝试各种不同的使用方法,以寻找减少人员搬运工作的最佳用法。”
宫本所长乐观地说,“投入使用后,它能完成相当于一个搬运工的工作。虽然投入了巨大的投资,但这让从来没有使用过机器人的我们有机会学习地图功能和其他技术。”
人机协作,分工明确
为了“OTTO100”,中心在每个区域安装了三个WiFi接入点,并在站点间自动运行。通过WiFi连接,工人可以确定它的当前位置,并且远程控制它,但由于信号的关系,它只能进行直线移动,这让人十分苦恼。尽管该中心试图增加信号接入点,但是效果仍不理想。
“在投入使用后我们注意到,由于现场大量便携式终端,无线信号不可避免地会受到干扰。所以我们尽量只走没有信号干扰的路线,避免造成工人负担。”中村先生介绍道。
相比之下,“OMRONLD”目前以独立的形式运行,中心正在考虑检查网络环境,研究是否可以为其提供WiFi环境,让多台搬运机器人一同运行。如果可以进行中央控制和远程遥控指示的话,机器人在现场的可用性会大大提高。
“网购市场每年扩大,如果我们不创新,随着工作量进一步扩大,工作肯定会受到影响。因此我们必须不断消除作业现场的缺陷,同时迎接新的挑战。虽然也会面临失败,但如果不努力改善,便会因为无法适应业务量的增长而给顾客带来麻烦。因此我们正在努力采取措施。”宫本所长补充道。
下一个迫在眉睫的挑战则是上文提到过的包装工作。
大野先生表示,“在分拣领域,人类在机动性、应变能力等方面都明显优于机器人,因此我们对今后的机器人技术革新寄予厚望。另一方面,分拣后续的手工包装作业速度跟不上拣选速度,包装作业的自动化也势在必行。因此,在‘I-Pack’之后,我们正考虑安装第二台自动打包机。”
大野泰继先生
“如今在物流作业领域中,人类比机器的能力要强得多。所以我们把机器能完成的任务交给机器,人则专注于只有人才能完成的任务。这样进行工作的同时,也能得到一些新的改进灵感。我们希望自动化可以让人花更多的时间在人类有优势的工作上。”宫本所长最后说道。他的眼神似乎已经展望到了必将到来的未来。
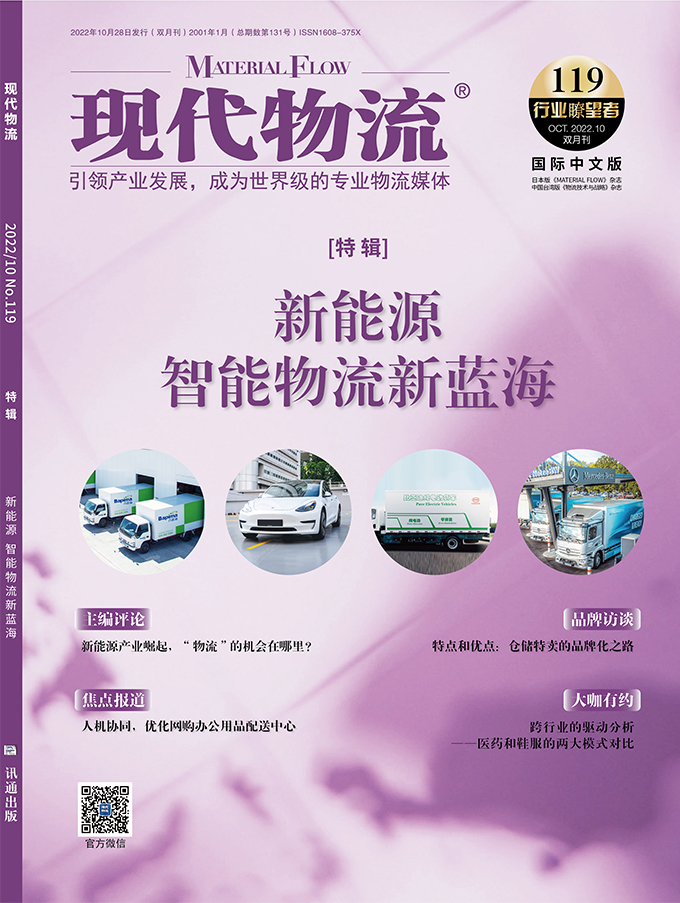
文章精选/现代物流-119期