【导语】本文介绍了从丰田生产方式、精益思想到精益供应链的发展与蜕变历程,接着从精益五大核心观念的角度来说明管理者如何打造具有精益思维的供应链,让企业们对于精益供应链的发展历程与来龙去脉除不仅有清晰的认识,并对于如何打造精益供应链掌握最重要的核心精神。

精益供应链(Lean Supply Chains),来自于美国精益生产及思想,源于日本丰田汽车的丰田生产方式(Toyota Production System, TPS),指将从产品设计到成品交付,整个过程所必需的步骤和参与企业整合,以快速回应客户多变的需求。其核心是消除企业内或企业间的浪费,以最少的资源最大程度上满足客户需求。精益供应链是减少浪费、降低成本、缩短操作周期、提供强化的客户价值从而增强企业竞争优势的一种有效的方法。
丰田生产方式
丰田生产方式(Toyota Production System,TPS),是由丰田提出的一个整合的生产系统,包含管理理念和实践。该系统为后来美国“精益生产及思想”的先驱,但该系统不是一成不变的,而是时时在进步的生产方式。丰田员工们每天持续思考该如何才能迅速提供消费者更加物美价廉的商品,改变制造、物流等方式,以适应时代的需求不断革新。
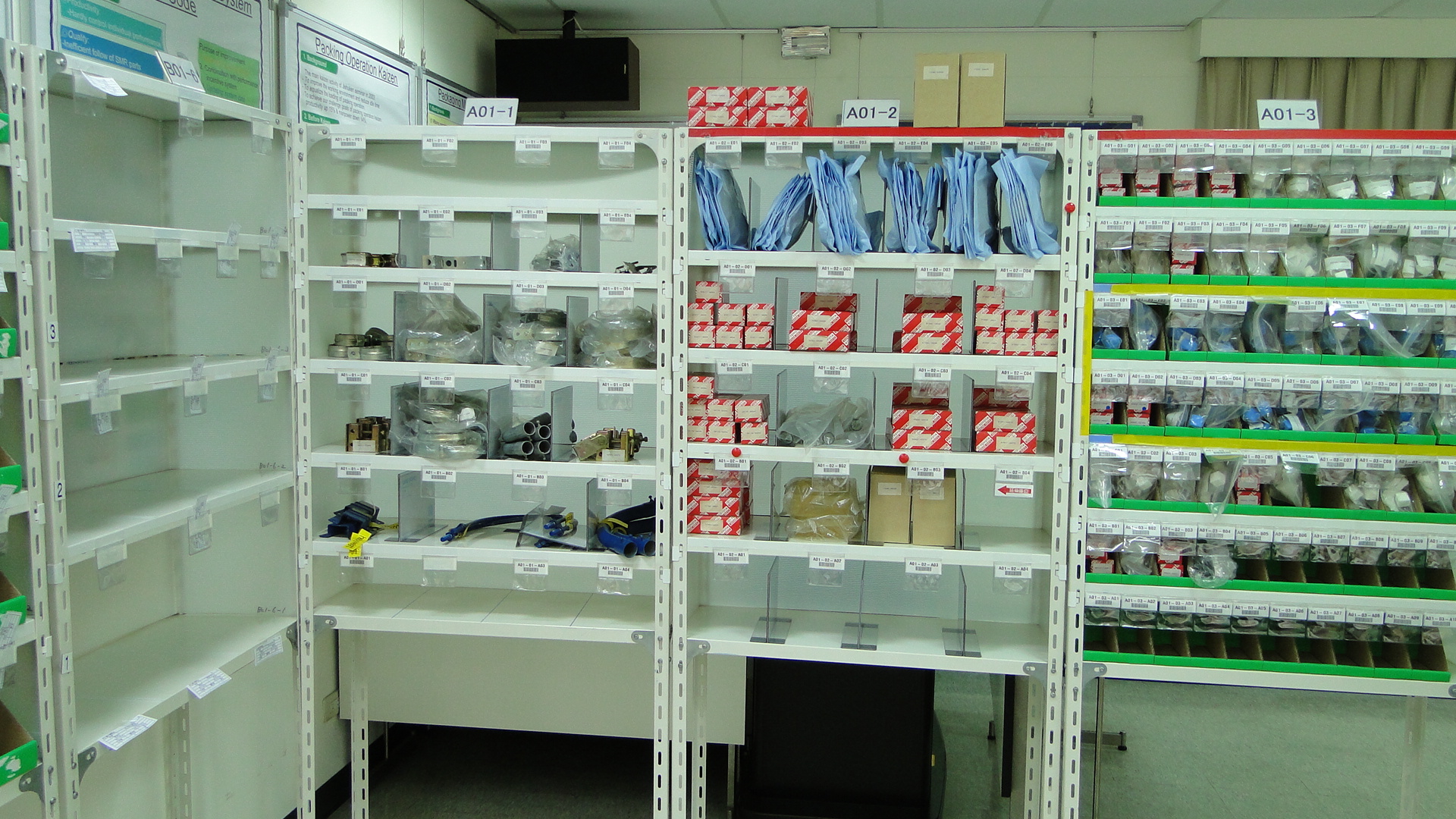
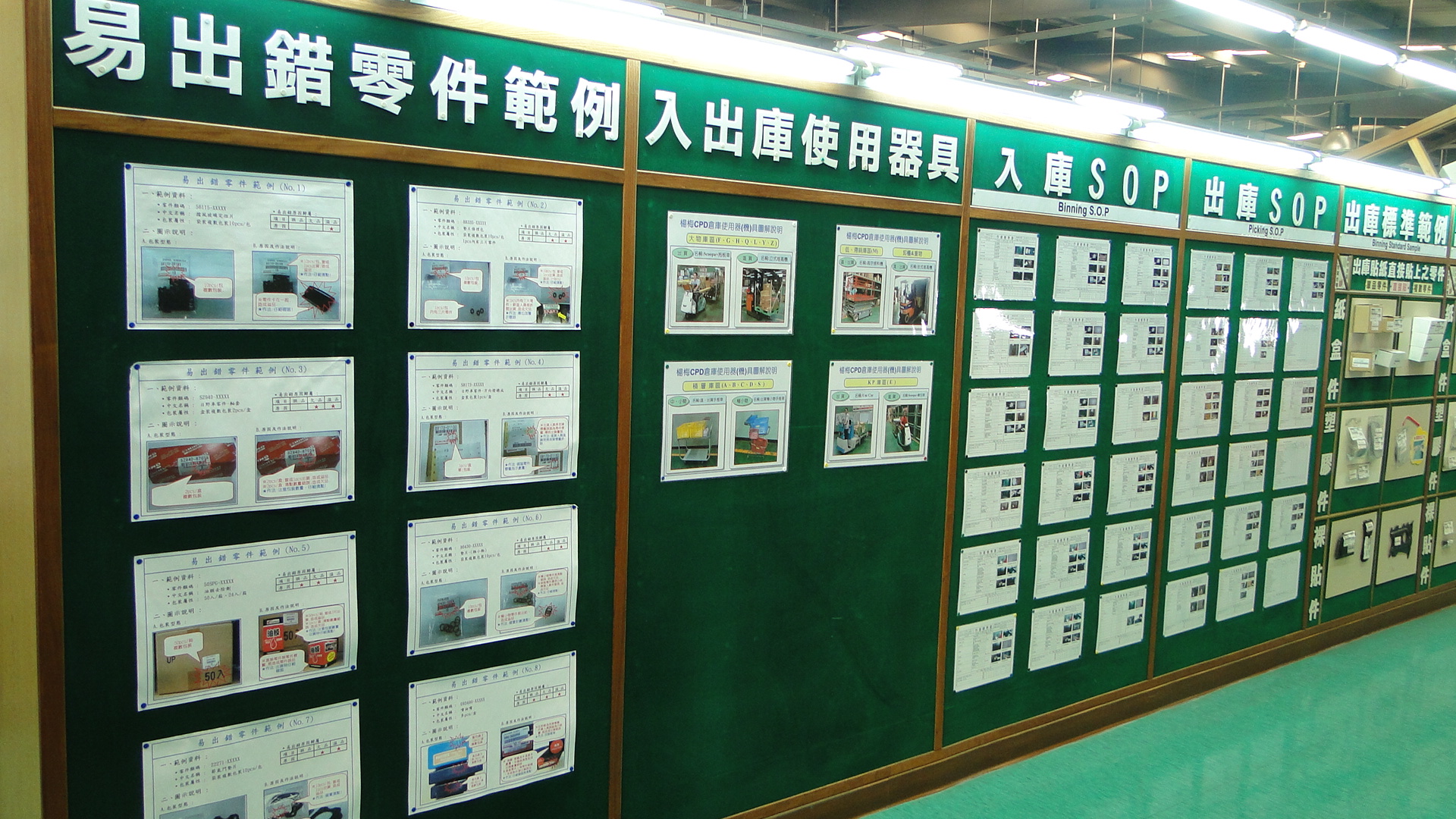
丰田生产方式有两大支柱,一为突显浪费与异常的自动化(Jidoka),二为刚好实时的及时化Just in Time (Just in Time,JIT),兹说明如下:
突显浪费与异常的自动化
这是一种杜绝不良品的质量控制方法,不但会自动生产所需要的零件,也会在发现质量问题时自动停止,避免生产出大量不良品,增加浪费。自动停止生产线的精髓,在于创造一个使问题自动浮现并及时解决的机制,从而使生产有效地持续运作。若进一步将此理念延伸到企业内的生产现场,就是杜绝不良品流到下一工序,而若将此理念进一步扩伸到企业间,则是指避免不良品在上游供应商和下游客户之间流通,造成整体供应链的损失。
刚好实时的及时化Just in Time
Just in Time的理念是保持物流和信息流在生产中的同步,实现“按需生产”,也就是追求一种库存数量最小、甚至无库存的方式。这种理念可以减少库存、缩短工时、降低成本、提高生产效率。鉴于当时日本国内市场环境、劳动力以及二次世纪大战之后资源短缺等原因,日本必需采取一种更灵活,更能适应市场需求并能够提高产品竞争力的生产方式,即由下游客户订单拉动,利用需求拉动把供、产、销紧密地衔接起来,这样能使库存和半成品大为减少,进而提高了生产效率。
随着互联网技术的广泛运用,企业已经能够将Just in Time扩展延伸至组织外,通过要求供应商实时提供原材料,实现JIT生产,公司的订货、配送等流程变得更快捷、更灵活、更高效,形成连结上游供应商和下游客户的供需网络(供应链)。

综合自动化与Just in Time构成的丰田生产方式的主要目标,就是杜绝一切的浪费(muda)。当时丰田生产现场存在着以下浪费,谓之“丰田七大浪费”:
1. 等待的浪费;
2. 搬运的浪费;
3. 不良品的浪费;
4. 动作的浪费;
5. 加工的浪费;
6. 库存的浪费;
7. 制造过多或过早的浪费。
“丰田七大浪费”不仅能够凸显生产现场的问题,还可以站在更高的角度与整体系统的角度来观察,从而审视处于供应链中的的上游供应商和下游客户之间是否也同样存在着各种浪费。
改变世界的机器——精益思想
丰田生产方式使丰田汽车大大降低成本和缩短交货期,同时又提高产品品质。由于无论市场是繁荣还是低迷,丰田的表现都持续亮眼,因此1985年美国麻省理工学院在一项名为“国际汽车计划”的研究项目中,两位教授吉姆·沃马科(Jim Womack) 与丹尼尔·琼斯(Daniel Jones)在研究以日本丰田汽车为首的少数日本企业管理模式后,认为日本丰田汽车的生产方式是最适用于现代制造企业的一种生产组织管理方式,称之为“精益生产(Lean Production)”,以针对美国大量生产方式过于臃肿的弊病。
Lean是指没有多余的脂肪,对应到企业的经营上,则是没有任何资源浪费的现象,流程运作顺畅,以最小的投入创造更多利润,并且可以将Lean 的含义,从制造业的现场生产引用到服务业的企业经营上,故目前在各行各业都如雨后春笋般地运用精益理念及思想。
1996年,两位教授进一步加深精益思想(Lean Thinking),阐述更为完整的精益理念。精益不只是改善的工具,更是一套完整的企业管理思维;精益思想是一个企业如何追求以最小的投资,为客户创造最大价值的思维方式;它并非只着眼于局部的减少浪费及提高效率,更重要的是帮助企业重新思考如何提高企业整体的营运效率,所以精益理念及思想成为了全世界企业学习与取经的目标。

其核心思想有二:
要通过客户的眼睛来确认价值
精益就是以客户的需求为主,消除各种流程中的浪费;采取客户“后拉式”(pull) 生产或服务,而非以预测为主的“推式”(push) 生产或服务。要从客户端出发,通过客户的眼睛来确认价值,并且避免浪费。此理念点出精益的两个关键字:“价值”与“浪费”。不能增加客户价值的活动,就是浪费,唯有充分了解客户的价值,才能分辨何谓浪费、何谓有价值,进而将资源投入在提升客户价值的活动与流程上。其强调,要达到总体经营效益的提升,前提是要能够为客户提供更多的价值,如果不是从这个方向出发,反而会制造出更多的浪费。
精益思想贯穿整个流程
精益思想具有系统思维,其着眼于整个流程并消除各种流程中的浪费,故只要有流程,精益在各行各业都能运用,所以不只涵盖企业内的流程,并能推广到供应链之间。另外,精益理念虽始于制造业,但不是只有制造业才需要推动精益,现在服务业也纷纷将精益导入于服务流程中。
精益的核心价值,通过其他学者再诠释,或结合其他科学方法,衍生出了精益企业体 (Lean Enterprise)、精益整合 Lean Integration)、精益文化 (Lean Culture)、精益组织(Lean Organization)、精益六标准差管理等等。精益基本上已经延伸至公司文化或公司治理等层面,也因此称为精益思想(Lean Thinking)。
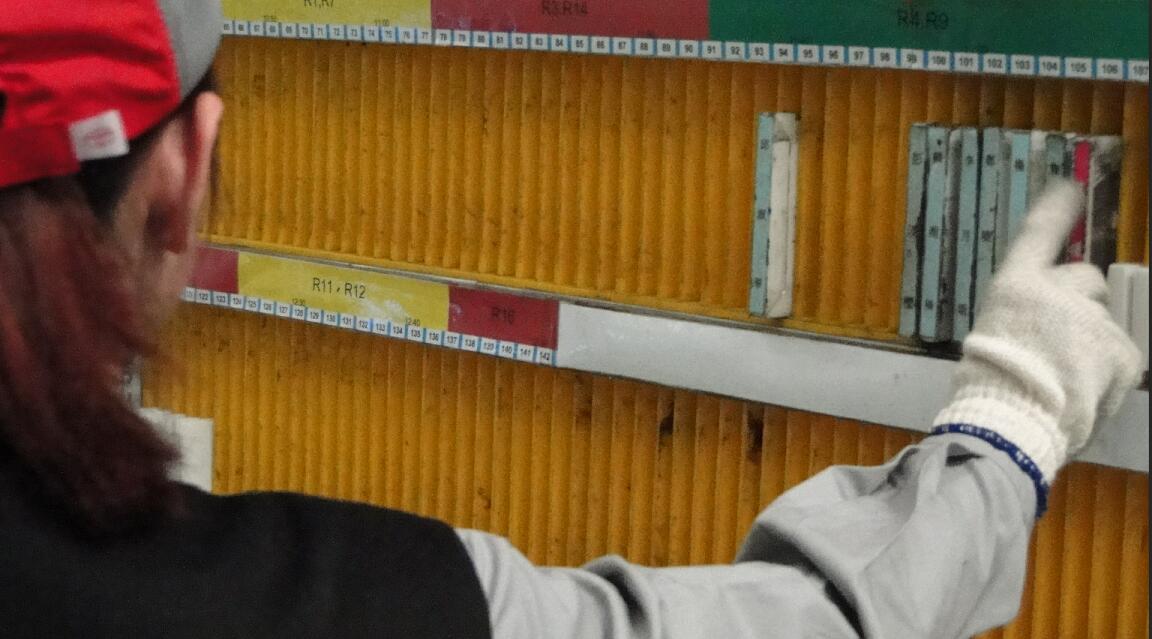
打造具有Lean Thinking的精益供应链
精益供应链(Lean Supply Chains),源于以上的丰田生产方式与精益思想。是指对整个供应链的环节包括上游供应商和下游客户进行优化和改造,免除不必要的步骤、耽搁以及消耗,消除供应链间企业的浪费,用最低的成本满足最大程的客户需求的一系列对供应链的计划、实施和控制的过程。
精益供应链管理要求上下游企业间共同努力消减整个流程的成本和浪费,单个行业虽能够在内部实施精益,但精益供应链要求上下游企业要共同合作,协调一致,才能建立精益供应链。
目前行业内的各种专有名词及手法名目繁多,但是只要掌握核心的观念与精神,其实各种手法只是达成打造精益供应链的工具之一,只要能掌握其精神,便能提纲契领,掌握重点。
精益思想主要依循Womack and Jones所提出之五大核心观念(五项步骤):
1.价值(Value)
2.价值溪流(Value stream)
3.畅流(Flow)
4.后拉(Pull)
5.完善(Perfection)
步骤一:定义价值 (Specify value)
精益思想的关键起点在于价值 (Value),现场改善或企业经营有两种活动在进行,即“有或无附加价值的”,为避免浪费发生,要思考任何动作是否有意义,并且从最终客户的角度来确认价值,在何处可创造出价值,再考量产品或服务是否符合客户需求。精益要求所有环节的动作应从客户的角度出发,来衡量企业活动是否有对客户有价值,当一个生产或服务的动作只是习以为常,而不是以满足客户为出发点所建立,即视为浪费,应予以消除。
步骤二:确认价值流动(Identify the value stream)
价值流动为带给企业自身客户或供应链客户的特定产品及或服务所需的所有增值型 (value-added) 及非增值型(non value-added) 活动。为确认价值流动,首先必须了解生产或服务中所有经过的步骤,通过了解各个步骤,才可建立出价值流动图 (Value Stream Mapping)。价值流动图是通过生产或服务过程的全部活动,只要有一项为客户生产的产品,就有一个价值流。每项产品类别均可视为一个价值流动图。价值流动图可视为改善生产或服务过程的一种共通语言,透过价值流动图可以观察流程内外的整个价值流动的流动过程,诸如从客户接收订单开始,往前拓展到组织内部生产的过程,以至成品入库的状况,直到交货的过程,甚或可再往前伸展到原物料的供应。建立价值流动图后,即可分析所有生产或服务活动的价值。确认价值流动图的目的,在于整体的检视其生产或服务步骤,并确认每个步骤是否是为满足最终客户需求所建立。
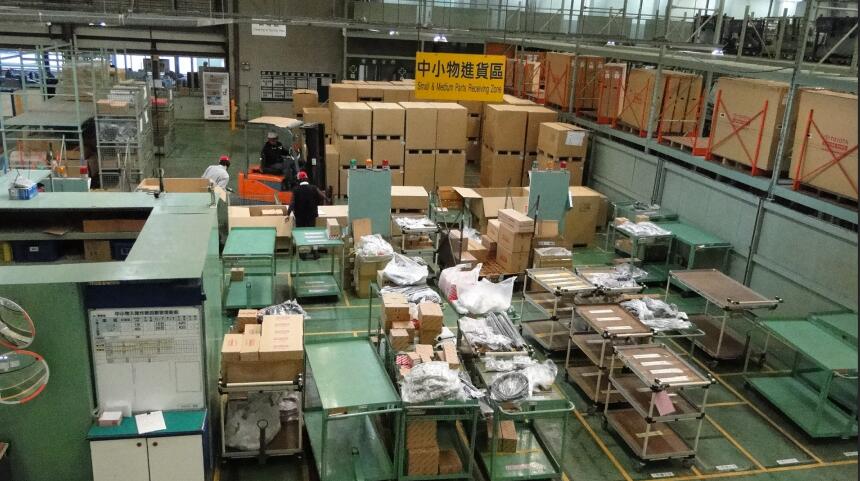
步骤三:畅流 (Flow)
建立实况的价值流动图并确认每条流程的价值后,就可以进行“畅流”。畅流的目的是为让实况价值流动中,属于有价值的步骤能顺畅有效率的进行,并去除没有价值的步骤,以减少阻碍与浪费。在畅流中,除了改善没有价值的步骤,还要注意分批与等待(batch and wait),无论是生产或服务,往往受一批量所限制,货物必须一批一批的移动,往往会产生等待与许多不必要的浪费,而本来可以自由运作的时间,被切成以块状分布,错误也无法立即发现。畅流即要改变此类模式,减少半成品与等待,使流程能顺畅流动,。
步骤四:由客户来拉动 (Custom pull)
所有生产或服务活动应配合客户需求来建立价值,所以由需求拉动生产或服务节奏,配合需求产生,才从事生产或服务。拉动式生产可由客户需求来拉动生产或服务,再由后道工序拉动前道工序,前道工序再拉动仓库与上游供应商。
步骤五:完善 (Perfection)
在完成改善后,精益的过程应再回到第一步骤:“定义价值”重新开始,通过一次又一次的执行,反复地用价值流程分析方法找出隐藏于更深处的浪费,并作进一步的改进,以此期望能生产更贴近客户需求的产品及服务,而此良性循环即为追求尽善尽美的过程。
以上内容说明了管理者如何打造具有精益思维的供应链,包括对于精益供应链的发展历程与来龙去脉以及如何打造精益供应链都有了详细的解析。对于如何打造出具有Lean Thinking的精益供应链,需要的是企业们在生产或服务时时Lean Thinking,并遵循这精益思想的五大核心观念(五项步骤)。
………………………………………………………………………………………
参考资料:
任恒毅、廖秀姬,精益生产价值溪流程改善方法之实证研究,质量学报。
台湾全球商贸运筹发展协会,物流与运筹管理。
MBA智库百科,https://wiki.mbalib.com
百度百科,https://baike.baidu.com
维基百科,https://zh.wikipedia.org


精益供应链(Lean Supply Chains),来自于美国精益生产及思想,源于日本丰田汽车的丰田生产方式(Toyota Production System, TPS),指将从产品设计到成品交付,整个过程所必需的步骤和参与企业整合,以快速回应客户多变的需求。其核心是消除企业内或企业间的浪费,以最少的资源最大程度上满足客户需求。精益供应链是减少浪费、降低成本、缩短操作周期、提供强化的客户价值从而增强企业竞争优势的一种有效的方法。
丰田生产方式
丰田生产方式(Toyota Production System,TPS),是由丰田提出的一个整合的生产系统,包含管理理念和实践。该系统为后来美国“精益生产及思想”的先驱,但该系统不是一成不变的,而是时时在进步的生产方式。丰田员工们每天持续思考该如何才能迅速提供消费者更加物美价廉的商品,改变制造、物流等方式,以适应时代的需求不断革新。
突显浪费与异常的自动化
这是一种杜绝不良品的质量控制方法,不但会自动生产所需要的零件,也会在发现质量问题时自动停止,避免生产出大量不良品,增加浪费。自动停止生产线的精髓,在于创造一个使问题自动浮现并及时解决的机制,从而使生产有效地持续运作。若进一步将此理念延伸到企业内的生产现场,就是杜绝不良品流到下一工序,而若将此理念进一步扩伸到企业间,则是指避免不良品在上游供应商和下游客户之间流通,造成整体供应链的损失。

刚好实时的及时化Just in Time
Just in Time的理念是保持物流和信息流在生产中的同步,实现“按需生产”,也就是追求一种库存数量最小、甚至无库存的方式。这种理念可以减少库存、缩短工时、降低成本、提高生产效率。鉴于当时日本国内市场环境、劳动力以及二次世纪大战之后资源短缺等原因,日本必需采取一种更灵活,更能适应市场需求并能够提高产品竞争力的生产方式,即由下游客户订单拉动,利用需求拉动把供、产、销紧密地衔接起来,这样能使库存和半成品大为减少,进而提高了生产效率。
随着互联网技术的广泛运用,企业已经能够将Just in Time扩展延伸至组织外,通过要求供应商实时提供原材料,实现JIT生产,公司的订货、配送等流程变得更快捷、更灵活、更高效,形成连结上游供应商和下游客户的供需网络(供应链)。

1. 等待的浪费;
2. 搬运的浪费;
3. 不良品的浪费;
4. 动作的浪费;
5. 加工的浪费;
6. 库存的浪费;
7. 制造过多或过早的浪费。
“丰田七大浪费”不仅能够凸显生产现场的问题,还可以站在更高的角度与整体系统的角度来观察,从而审视处于供应链中的的上游供应商和下游客户之间是否也同样存在着各种浪费。
改变世界的机器——精益思想
丰田生产方式使丰田汽车大大降低成本和缩短交货期,同时又提高产品品质。由于无论市场是繁荣还是低迷,丰田的表现都持续亮眼,因此1985年美国麻省理工学院在一项名为“国际汽车计划”的研究项目中,两位教授吉姆·沃马科(Jim Womack) 与丹尼尔·琼斯(Daniel Jones)在研究以日本丰田汽车为首的少数日本企业管理模式后,认为日本丰田汽车的生产方式是最适用于现代制造企业的一种生产组织管理方式,称之为“精益生产(Lean Production)”,以针对美国大量生产方式过于臃肿的弊病。

Lean是指没有多余的脂肪,对应到企业的经营上,则是没有任何资源浪费的现象,流程运作顺畅,以最小的投入创造更多利润,并且可以将Lean 的含义,从制造业的现场生产引用到服务业的企业经营上,故目前在各行各业都如雨后春笋般地运用精益理念及思想。
1996年,两位教授进一步加深精益思想(Lean Thinking),阐述更为完整的精益理念。精益不只是改善的工具,更是一套完整的企业管理思维;精益思想是一个企业如何追求以最小的投资,为客户创造最大价值的思维方式;它并非只着眼于局部的减少浪费及提高效率,更重要的是帮助企业重新思考如何提高企业整体的营运效率,所以精益理念及思想成为了全世界企业学习与取经的目标。

要通过客户的眼睛来确认价值
精益就是以客户的需求为主,消除各种流程中的浪费;采取客户“后拉式”(pull) 生产或服务,而非以预测为主的“推式”(push) 生产或服务。要从客户端出发,通过客户的眼睛来确认价值,并且避免浪费。此理念点出精益的两个关键字:“价值”与“浪费”。不能增加客户价值的活动,就是浪费,唯有充分了解客户的价值,才能分辨何谓浪费、何谓有价值,进而将资源投入在提升客户价值的活动与流程上。其强调,要达到总体经营效益的提升,前提是要能够为客户提供更多的价值,如果不是从这个方向出发,反而会制造出更多的浪费。
精益思想贯穿整个流程
精益思想具有系统思维,其着眼于整个流程并消除各种流程中的浪费,故只要有流程,精益在各行各业都能运用,所以不只涵盖企业内的流程,并能推广到供应链之间。另外,精益理念虽始于制造业,但不是只有制造业才需要推动精益,现在服务业也纷纷将精益导入于服务流程中。
精益的核心价值,通过其他学者再诠释,或结合其他科学方法,衍生出了精益企业体 (Lean Enterprise)、精益整合 Lean Integration)、精益文化 (Lean Culture)、精益组织(Lean Organization)、精益六标准差管理等等。精益基本上已经延伸至公司文化或公司治理等层面,也因此称为精益思想(Lean Thinking)。
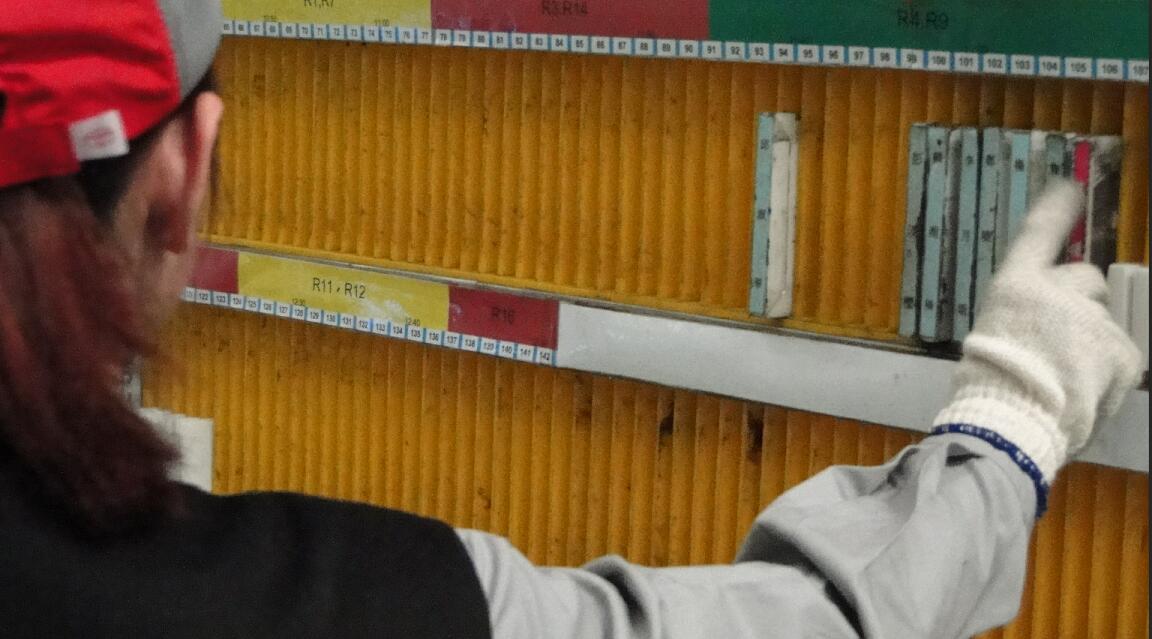

打造具有Lean Thinking的精益供应链
精益供应链(Lean Supply Chains),源于以上的丰田生产方式与精益思想。是指对整个供应链的环节包括上游供应商和下游客户进行优化和改造,免除不必要的步骤、耽搁以及消耗,消除供应链间企业的浪费,用最低的成本满足最大程的客户需求的一系列对供应链的计划、实施和控制的过程。
精益供应链管理要求上下游企业间共同努力消减整个流程的成本和浪费,单个行业虽能够在内部实施精益,但精益供应链要求上下游企业要共同合作,协调一致,才能建立精益供应链。
目前行业内的各种专有名词及手法名目繁多,但是只要掌握核心的观念与精神,其实各种手法只是达成打造精益供应链的工具之一,只要能掌握其精神,便能提纲契领,掌握重点。
精益思想主要依循Womack and Jones所提出之五大核心观念(五项步骤):
1.价值(Value)
2.价值溪流(Value stream)
3.畅流(Flow)
4.后拉(Pull)
5.完善(Perfection)
步骤一:定义价值 (Specify value)
精益思想的关键起点在于价值 (Value),现场改善或企业经营有两种活动在进行,即“有或无附加价值的”,为避免浪费发生,要思考任何动作是否有意义,并且从最终客户的角度来确认价值,在何处可创造出价值,再考量产品或服务是否符合客户需求。精益要求所有环节的动作应从客户的角度出发,来衡量企业活动是否有对客户有价值,当一个生产或服务的动作只是习以为常,而不是以满足客户为出发点所建立,即视为浪费,应予以消除。
步骤二:确认价值流动(Identify the value stream)
价值流动为带给企业自身客户或供应链客户的特定产品及或服务所需的所有增值型 (value-added) 及非增值型(non value-added) 活动。为确认价值流动,首先必须了解生产或服务中所有经过的步骤,通过了解各个步骤,才可建立出价值流动图 (Value Stream Mapping)。价值流动图是通过生产或服务过程的全部活动,只要有一项为客户生产的产品,就有一个价值流。每项产品类别均可视为一个价值流动图。价值流动图可视为改善生产或服务过程的一种共通语言,透过价值流动图可以观察流程内外的整个价值流动的流动过程,诸如从客户接收订单开始,往前拓展到组织内部生产的过程,以至成品入库的状况,直到交货的过程,甚或可再往前伸展到原物料的供应。建立价值流动图后,即可分析所有生产或服务活动的价值。确认价值流动图的目的,在于整体的检视其生产或服务步骤,并确认每个步骤是否是为满足最终客户需求所建立。
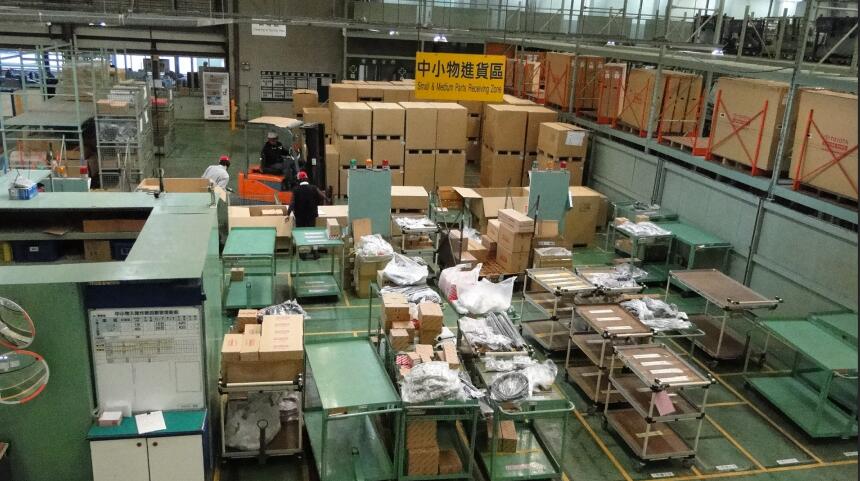

步骤三:畅流 (Flow)
建立实况的价值流动图并确认每条流程的价值后,就可以进行“畅流”。畅流的目的是为让实况价值流动中,属于有价值的步骤能顺畅有效率的进行,并去除没有价值的步骤,以减少阻碍与浪费。在畅流中,除了改善没有价值的步骤,还要注意分批与等待(batch and wait),无论是生产或服务,往往受一批量所限制,货物必须一批一批的移动,往往会产生等待与许多不必要的浪费,而本来可以自由运作的时间,被切成以块状分布,错误也无法立即发现。畅流即要改变此类模式,减少半成品与等待,使流程能顺畅流动,。
步骤四:由客户来拉动 (Custom pull)
所有生产或服务活动应配合客户需求来建立价值,所以由需求拉动生产或服务节奏,配合需求产生,才从事生产或服务。拉动式生产可由客户需求来拉动生产或服务,再由后道工序拉动前道工序,前道工序再拉动仓库与上游供应商。
步骤五:完善 (Perfection)
在完成改善后,精益的过程应再回到第一步骤:“定义价值”重新开始,通过一次又一次的执行,反复地用价值流程分析方法找出隐藏于更深处的浪费,并作进一步的改进,以此期望能生产更贴近客户需求的产品及服务,而此良性循环即为追求尽善尽美的过程。
以上内容说明了管理者如何打造具有精益思维的供应链,包括对于精益供应链的发展历程与来龙去脉以及如何打造精益供应链都有了详细的解析。对于如何打造出具有Lean Thinking的精益供应链,需要的是企业们在生产或服务时时Lean Thinking,并遵循这精益思想的五大核心观念(五项步骤)。
………………………………………………………………………………………
参考资料:
任恒毅、廖秀姬,精益生产价值溪流程改善方法之实证研究,质量学报。
台湾全球商贸运筹发展协会,物流与运筹管理。
MBA智库百科,https://wiki.mbalib.com
百度百科,https://baike.baidu.com
维基百科,https://zh.wikipedia.org
下一页