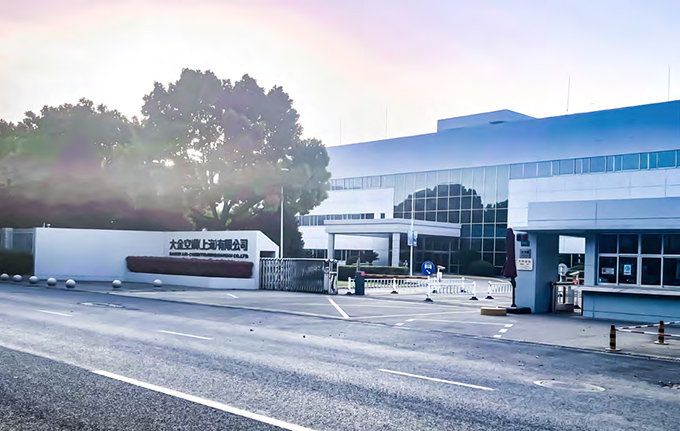
导语
“大金生产方式”,与耳熟能详的“丰田生产方式”之间,有何异同?
“精益”的核心
“精益”二字,对于供应链物流领域的从业者而言,一定不会陌生。2023年4月,本刊有幸参访了大金空调(上海)有限公司位于上海的工厂,从现场再度感受到了“精益”二字的精髓,和“大金生产方式”的奥秘。
首先,我们先回想一下,什么是精益?精益源于日本丰田汽车的丰田生产方式(Toyota Production System,TPS),指将从产品设计到成品交付,整个过程所必需的步骤和参与企业整合,以快速回应客户多变的需求。其核心是消除企业内或企业间的浪费,以最少的资源最大限度上满足客户需求。
丰田生产方式:杜绝一切的浪费
那什么是丰田生产方式?丰田生产方式是由丰田提出的一个整合的生产系统,包含管理理念和实践,该系统不是一成不变的,而是时时在进步的生产方式。丰田员工们每天持续思考该如何才能迅速提供消费者更加物美价廉的商品,改变制造、物流等方式,以适应时代的需求不断革新。
丰田生产方式有两大支柱,一为自働化(Jidoka),二为及时化Just in Time(Just in Time,JIT)。
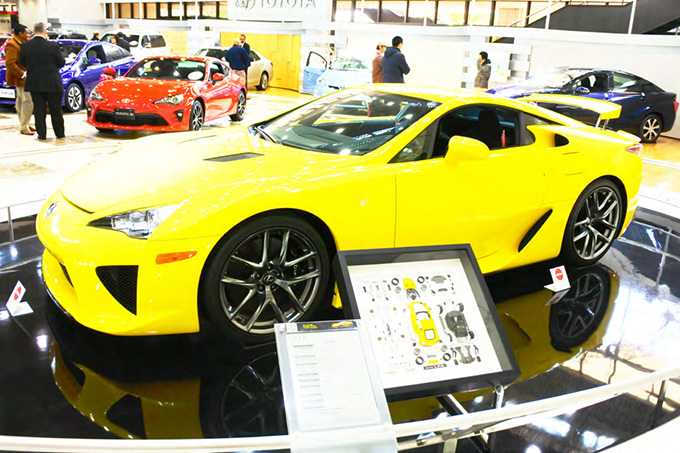
01自働化(Jidoka)而非自动化
注意,“自働化”而非“自动化”!这在参访的过程中,大金也特地强调了这一点,即需要包含人在内的自动化,人的判断力和人的控制力,能够判断本工序产品质量的合格与不合格和流程的正常与异常。
由此,以自働化为核心,能够诞生一种杜绝不良品的质量控制方法,不但会自动生产所需要的零件,也会在发现质量问题时自动停止,避免生产出大量不良品,增加浪费。若进一步将此理念延伸到企业内的生产现场,就是杜绝不良品流到下一工序,而若将此理念进一步扩伸到企业间,则是指避免不良品在上游供应商和下游客户之间流通,造成整体供应链的损失。
02Just in Time
Just in Time的理念是保持物流和信息流在生产中的同步,实现“按需生产”,也就是追求一种库存数量最小,甚至无库存的方式。这种理念可以减少库存、缩短工时、降低成本、提高生产效率。鉴于当时日本国内市场环境、劳动力以及二次世界大战之后资源短缺等原因,日本必需采取一种更灵活,更能适应市场需求并能够提高产品竞争力的生产方式,即由下游客户订单拉动,利用需求拉动把供、产、销紧密地衔接起来,这样能使库存和半成品大为减少,进而提高了生产效率。
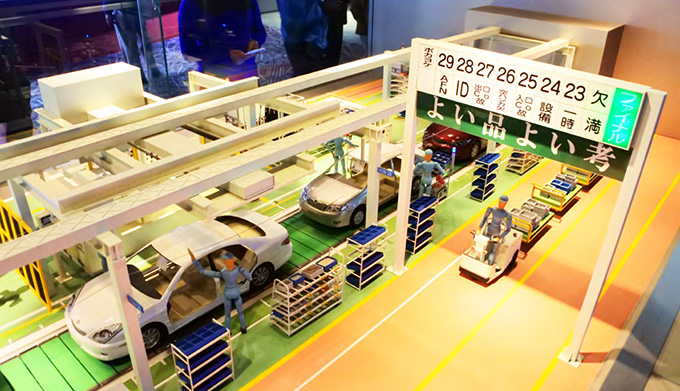
随着互联网技术的广泛运用,企业已经能够将Just in Time扩展延伸至组织外,通过要求供应商实时提供原材料,实现JIT生产,公司的订货、配送等流程变得更快捷、更灵活、更高效,形成连结上游供应商和下游客户的供需网络(供应链)。
而丰田生产方式的主要目标,就是杜绝一切的浪费。当时丰田生产现场存在着以下浪费,谓之“丰田七大浪费”:等待的浪费、搬运的浪费、不良品的浪费、动作的浪费、加工的浪费、库存的浪费、制造过多或过早的浪费。
“丰田七大浪费”不仅能够凸显生产现场的问题,还可以站在更高的角度与整体系统的角度来观察,从而审视处于供应链中的上游供应商和下游客户之间是否也同样存在着各种浪费。
似曾相识的大金生产方式
回到“大金生产方式”,从命名上看,PDS(Production of Daikin System)与“丰田生产方式(Toyota Production System,TPS)”相仿,其内核也是围绕“精益”二字展开,且构成PDS的两大支柱,同样在于“JIT”和“自働化”。
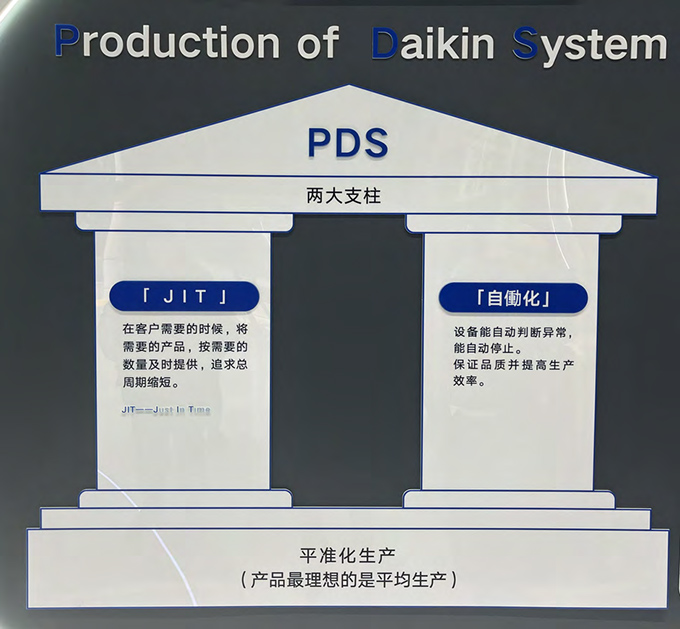
01“平准化生产”
而在这两大支柱之下,是以“平准化生产”为根基。大金认为,“产品最理想的是平均生产”。由于大金的产品SKU众多,如何平衡订单和生产效率,对于生产计划的制定和执行带来了极大的挑战。对此,大金强调总体效率最优,而不只是关注单个产线的效率。

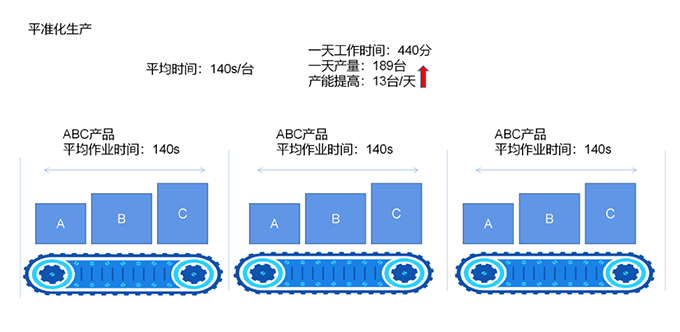
以A、B、C三个不同的SKU为例,A的订单需要6个小时完成,B需要8个小时,C需要10个小时,若采用传统单独专线生产的方式(前提是工厂为8小时工作制),只有B是恰好利用了生产时长。而若采用平准化生产方式,将品种混合于一个流(水线),以一台为单位进行多品种混合切换生产,则能够保证每天高效生产3个SKU,且不需要付出额外的成本。
同TPS一样,大金生产方式是通过“彻底的排除浪费”来达到成本降低的活动。为此,大金也提出了七大浪费:搬运浪费、加工本身浪费、生产不良浪费、能源浪费、动作浪费、等待浪费、库存浪费等。
02“目视化管理”和“三现主义”
同时,大金现场的“目视化管理”也值得称道。在各企业学习“精益”的过程中,“看板管理”是现场的标配,但是真的有学习到精髓吗?大金的目视化管理,同样是由各类看板组成,同时大金提出了“三现主义”,即现地、现物、现实,大金认为这是改善的根本。因此在大金现场,各个工位同样放置着信息庞大且能够一目了然的“看板”,通过这些看板,管理者能够在现场一目了然地了解每个工序、每道产线、每个工人的讯息,那这与现场管理者汇报有何不同?
“效率。”这是大金现场给出的回答。以产能为例,管理者首先能够通过位于工厂顶部的电子看板实时了解每一个生产计划的进度,那如果进度落后,就需要进一步了解原因并进行调整。传统的做法是通过询问“线长”等更基层的管理人员,而大金则是通过无处不在的实物看板,来看到该产线每个工序的工人数量、技能水平等细节信息。对于基层管理者而言,在得到生产计划之后,就需要根据计划配置所负责的工人数量,而通过看板,基层管理者可以直接了解工人信息,从而制定更合理的生产计划。“我们不仅要避免不合适的工人出现在不该出现的岗位,同时也要及时应对突发情况,这些看板的存在,能够让我们主动快速地进行调整,而不是被动等待讯息反馈后再调整。”
人才培养是根基
而在这一切的基础,是对于“人才”的培养。大金致力于打造坚韧且不可动摇的制造团队,即以人才培养为重点,打造充满“自主·清新·活力·激情”的,具有“坚定信念、挑战意识”的制造业团队。
那大金是如何做的?大金将自身培训基地以“道场”命名。在道场,大金有着每个工序的培训实操设备,大金认为,员工技能的掌握需要不断反复地磨炼,无论是新老员工,在无法达到生产需求时,就会被送到道场进行训练,大金不轻易放弃员工,而道场就是来帮助员工更长久地留在大金。道场中最令人惊奇的是一条乐高组装流水线。据介绍,这条流水线是用来培养和训练生产小组的协同能力的。大金通过不同款式乐高玩具组装的难度,定制了每个玩具组装的时间,而生产小组则需要根据“订单需求”,自行配料(选取乐高模块),分配工位,然后在规定的时间内完成成品组装。
01以“参与感”进行安全教育
大金对于安全的重视同样值得令人尊敬和学习。除了制定各种规章制度,更重要的是“参与感”。大金认为,口头教育虽然有作用,但是若能够让员工以体验的方式,亲身经历因不规范的穿着、作业和设备隐患等因素而导致的安全事故后果,会更让人印象深刻。
我们能够学到什么?
从大金出来,除了PDS带给我们的震撼,也值得让我们重新审视自己的企业,“精益”和TPS在如今的企业管理中十分常见,但是为何只有极少数的企业能够真正地做到,并转化为自己的“生产方式”?
在大金,一直秉持着“下道工序是上道工序的客户”的理念,这让每个员工在从事每个工作时,都秉持了“高品质交付”的理念,这是消除浪费的关键之一!而且,大金要求每一个命令和要求都要体现清晰完整,从而消除沟通浪费和因命令、要求不清晰带来的重复浪费,这一点恰恰是很多企业所欠缺的。因此,在大金,若发生对命令、要求执行不到位、错误执行时,首先会反思自身是否清晰地表达了要求。当然,制订一套合理的要求规则也是必要的,这也是为何大金的“目视化”管理能够真正实现高效的原因之一。
另外,“在问责员工有没有做好和做到之前,首先要问自己有没有做到和做好!”在大金,无论哪个环节、哪个级别的领导者,在面对错误时,首先反思自身有没有出现错误的示范和指导,这种自上而下的自我认知和管理能力,是推动TPS不断前进的关键。
大金一直奉行“造物亦造人,育人亦育己”的理念。这是大金对于自身的核心认知,看上去大金生产方式更像是TPS在空调制造领域中的落地,包括“持续改善”和“一切都是恰到好处”等理念。不过,大金也有着自己的理解,大金亦认为,“做了改善不一定是成功”,“回到原点也是另外一种成功”来勉励自身。
“今天不代表大金,明日正在走来”,“用空气创造答案”的大金,也将持续书写属于自己的传奇故事。